-
Lifting Equipment
Lifting Equipment
- Chain Hoists
-
Wire Rope Hoists & Winches
- Hand Operated Wire Rope Winches and Hoists
- Cable Pullers / Hoists, Wire Rope Manual Operation
- Electric Winches and Hoists, AC (Mains Powered)
- Scaffold Hoists & Accessories
- Overhead Wire Rope Crane Hoists
- Hydraulic Wire Rope Winches & Hoists
- Pneumatic Wire Rope Air Winches / Hoists (Lifting and Pulling)
- Vehicle Mounted Winches
- Tractel Wire Rope & Accessories
-
General Lifting Equipment
- Soft Lifting Slings
- Lifting Chain Slings
- Wire Rope Slings & Assemblies
- Lifting Shackles
- Eye Bolts and Nuts
- Weld-on Lifting Eyes and Lashing Points
- Lifting & Pulling Clamps
- Lifting Beams & Spreader Beams
- Precast Concrete Lifting
- Lifting Magnets, Permanent, Battery Electric and Manual
- Beam Trolleys and Crane Bridges, Push, Geared & Electric
- Equipment Identification Tags
-
Rigging Equipment
- Master Ring & Load Suspension Eyes
- Lifting & Rigging Hooks
- Turnbuckles & Rigging Screws
- Wire Rope Accessories and Fittings
- Snatch Blocks, Sheave Blocks and Crane Pulley Blocks
- Pulley Sheaves
- Lifting & Rigging Swivels - Eye, Hook & Shackle
- Load Restraint Equipment
- General Rigging Accessories
- Crosby Lifting & Rigging
-
Cranes & Gantry Systems
- Portable Davit Arms
- Swing Jib Cranes - Installed Floor & Wall Cranes
- Portable/Mobile Free-standing Swing Jib Cranes
- Aluminium Gantry Cranes
- Steel Gantry Cranes
- Fixed Steel Gantry Systems
- Shearlegs, Tripods & Quadpods
- Overhead Crane Systems
- Portable Shop-Floor/Workshop/Garage Cranes
- Counterbalance Floor, Workshop Cranes
- Scaffolding Runway Beam Systems
-
Material Handling & Jacking Equipment
- Machinery & Load Moving Skates
- Hydraulic Cylinders & Pumps
- Lifting Jacks
- Manhole Cover Lifters
- Hydraulic Pull Cylinders
- Hand Operated Pallet Trucks, Pump Trucks
- Stacker Trucks, Materials Lifts, Manual and Electric
- Genie and Counterbalance Materials Lifters
- Scissor Lift Tables
- Drum Handling Equipment
- Crane Forks
- Load Weighing Equipment - Load Cells
- Tool Spring Balancers / Load Balancers
- Platform Trucks & Trolleys
-
Forklift Truck Attachment
- Fork Mounted Man Riding Baskets
- Environment & Waste Handling Attachments
- Fork Lift Truck Mounted Drum Handling Attachments
- Fork Mounted Jib and Hook Attachments
- Fork Truck Booms & Tines
- Stainless Steel Forklift Attachments
- Forklift Truck Fork Extensions
- Multi Fork Attachments
- Fork Truck Scoop Attachments
- Big Bag Fork Truck Attachment
- Closed Base Coil Support Attachments
- Forklift Fork Protection Sleeves
- Snow Plough Fork Lift Truck Attachments
- Other Forklift Truck & Telehandler Attachments
- Specialist Lifting Equipment
- Access and Safety Related
- Workshop and Shop Floor
- Screwjacks & Actuators
-
Height Safety
Height Safety Equipment
-
Fall Arrest and Height Safety Harnesses
- General Use Harnesses EN361
- Work Positioning Harnesses EN361 & EN358
- Rope Access Harnesses
- Rescue Harnesses EN1497 & EN361
- Ladies & Childrens Harnesses
- Hi Vis Jacket/Vest Harnesses
- Welders Harnesses
- ATEX (Anti-Static) Harnesses
- Linesman Harnesses
- Oil Derrick Harnesses
- Sport Climbing Harnesses
- Tree Surgeon Positioning Harnesses
- Sit and Chest Harnesses. EN361 EN356 & EN831
- Work Positioning & Restraint Belts EN358
- Fall Arrest, Restraint and Positioning Lanyards
- Height Safety and Fall Arrest Kits
- Inertia Reels and Retrieval Blocks
-
Confined Space and Rescue Systems
- Xtirpa Confined Space Davit Arm Systems and Components
- Sala Advanced Davit Arm Systems and Components
- Genesi Confined Space Systems
- Abtech Man-riding, Fall Arrest and Rescue Davits and Components
- Man-riding Hoists & Rescue Winches
- Fall Arrest & Rescue Tripods
- Fall Arrest Davit Arms & Posts for Working at Height
-
Fall Arrest & Man-riding Systems
- Manriding Systems, Baskets and Chairs
- Mobile Fall Arrest Gantries, Systems & Steps
- Rope Guided Fall Arresters (Steel & Synthetic Rope)
- Temporary Horizontal Fall Arrest Lifelines
- Vertical Fall Arrest Systems Permanently Installed
- Horizontal Fall Arrest Systems Permanently Installed
- Manriding Baskets Fork Truck and Overhead Crane
- Tank Side Entry and Vehicle Fall Arrest Systems
- Suspension Seats / Bosuns Chair Working at Height
- Collective Fall Arrest Systems
- Man-Riding Sheave Blocks
- Anchorage Devices
- Karabiners & Connectors
- Rescue, Evacuation & Rope Access
-
General Height Safety Gear
- Height Safety Accessories
- Industrial & Climbing Height Safety Helmets
- Synthetic Height Safety Rope & Anchorage Lines
- Height safety Pulley Wheels For Synthetic & Steel Wire Rope
- Black Height Safety Equipment & PPE
- Hot Work Equipment. Cutting, Grinding & Welding
- Cases, Bags, Backpacks, Holdalls. Height Safety Gear
- Telescopic Extension Pole for Height Safety Applications
- Wind Energy Height Safety Equipment
- Stainless Steel Fall Arrest Equipment
-
Fall Arrest and Height Safety Harnesses
- Home
- About Us
-
Contact
Get In Touch
The TIRFOR Principle
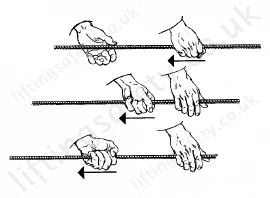
The general principle may be described as a «hand-over-hand» principle like a sailor pulling on a rope: while one hand pulls, the other one changes position in order to pull in turn.
The 2 jaw grips represent the 2 hands of the TIRFOR: they grip the wire rope without damaging it and alternately haul it during forward motion
and clamp it during reverse motion.
The effort is transferred to the jaws by means of 2 levers-one for forward motion and the other for reverse motion-which act by means of a cam
system on the keys that command the automatic clamping of the jaws on the rope.
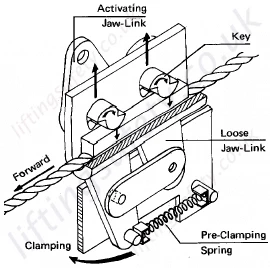
Functioning of the keys:
The jaw grips are made of 2 jaws which can be brought together (clamping) or separated (unclamping) by means of keys actuated by ievers called jaw-links.
When the jaw-link is moved to the left, the jaws are clamped on the wire rope in order to draw it or maintain it in position.
When the jaw-link is moved to the right, the jaws are unclamped in order to alow the wire rope to slip through but only in the direction opposed to the motion of the wire rope.
Forward Motion:
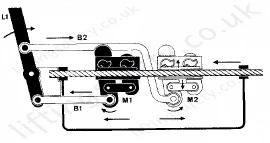
(the jaw which grips the wire rope is shown in black, the free-moving jaw is shown in white).
Forward motion is obtained by a to-and-fro motion of lever L1. If the lever is actuated to the right, grip M1, acted upon by connecting rod B1, clamps and draws the rope to the left. Simultaneously, grip M2 opens itself slightly and moves to the right.
If, thereafter, lever L1 is actuated to the left, the movements are simply reversed.
The power stroke lever L1 thus controls the progression of the rope from right to left, namely, the pulling or lifting of the load.
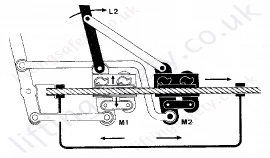
Reverse Motion:
Reverse motion is obtained by a to-and-fro motion of lever L2. If the lever is actuated to the right, grip M2 clamps and is drawn by the rope to the
right, while M1 opens itself slightly to let the cable glide while controlling its motion.
Inversely, if lever L2 is actuated to the left, grip M2 is clamped on the rope and grip M1 opens slightly to allow the rope glide under control.
This to-and-fro motion of lever L2 causes the progression of the rope from the left to right, hence the lowering of the load.
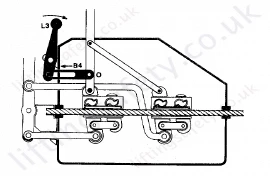
Release:
For ease of operation of the Tl RFOR, it must be possible to simultaneously open both jaws to introduce the rope, tension it or to disengage the machine.
To simultaneously release the jaws of the two grips, it is necessary to pull on the reverse mechanism at «O». A release system L3-B4 performs this function.
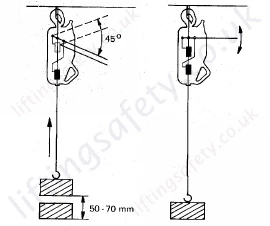
Precision:
To an angular motion of the front lever of 45° corresponds a load travel of 50 - 70 mm, depending on the TIRFOR model.
To an angular motion of the reverse lever of 45° corresponds a load travel of 75 - 100 mm, depending on the TIRFOR model.
If the motion of the front jaw lever or the rear jaw lever is arrested at a given position, the crankshaft-cam system acts as an equalizer and immediately distributes the load between the two jaws and maintains same in the position where it had stopped.
All this explains the unique precision of the TIRFOR machines.
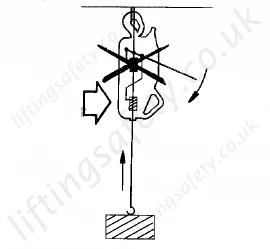
Safety:
If you operate a TIRFOR machine yourself in reverse, you will very quickly become aware of how perfectly safe it is. You will, of course, notice that
you must exert a certain effort on the lever. This effort corresponds to the effort required to force the wire rope through the unclamped jaw which
does not open but acts continuously as a secondary braking device.
The tests carried out in the presence of the representatives of the Underwriters Laboratories, Inc., Chicago have clearly demonstrated that if the clamped (black) jaw is damaged during its operation by an external object, the unclamped (white) jaw immediately steps in to control the load over a distance not exceeding the travel of the jaw, i.e., 5 cm.