-
Lifting Equipment
Lifting Equipment
- Chain Hoists
-
Wire Rope Hoists & Winches
- Hand Operated Wire Rope Winches and Hoists
- Cable Pullers / Hoists, Wire Rope Manual Operation
- Electric Winches and Hoists, AC (Mains Powered)
- Scaffold Hoists & Accessories
- Overhead Wire Rope Crane Hoists
- Hydraulic Wire Rope Winches & Hoists
- Pneumatic Wire Rope Air Winches / Hoists (Lifting and Pulling)
- Vehicle Mounted Winches
- Tractel Wire Rope & Accessories
-
General Lifting Equipment
- Soft Lifting Slings
- Lifting Chain Slings
- Wire Rope Slings & Assemblies
- Lifting Shackles
- Eye Bolts and Nuts
- Weld-on Lifting Eyes and Lashing Points
- Lifting & Pulling Clamps
- Lifting Beams & Spreader Beams
- Precast Concrete Lifting
- Lifting Magnets, Permanent, Battery Electric and Manual
- Beam Trolleys and Crane Bridges, Push, Geared & Electric
- Equipment Identification Tags
-
Rigging Equipment
- Master Ring & Load Suspension Eyes
- Lifting & Rigging Hooks
- Turnbuckles & Rigging Screws
- Wire Rope Accessories and Fittings
- Snatch Blocks, Sheave Blocks and Crane Pulley Blocks
- Pulley Sheaves
- Lifting & Rigging Swivels - Eye, Hook & Shackle
- Load Restraint Equipment
- General Rigging Accessories
- Crosby Lifting & Rigging
-
Cranes & Gantry Systems
- Portable Davit Arms
- Swing Jib Cranes - Installed Floor & Wall Cranes
- Portable/Mobile Free-standing Swing Jib Cranes
- Aluminium Gantry Cranes
- Steel Gantry Cranes
- Fixed Steel Gantry Systems
- Shearlegs, Tripods & Quadpods
- Overhead Crane Systems
- Portable Shop-Floor/Workshop/Garage Cranes
- Counterbalance Floor, Workshop Cranes
- Scaffolding Runway Beam Systems
-
Material Handling & Jacking Equipment
- Machinery & Load Moving Skates
- Hydraulic Cylinders & Pumps
- Lifting Jacks
- Manhole Cover Lifters
- Hydraulic Pull Cylinders
- Hand Operated Pallet Trucks, Pump Trucks
- Stacker Trucks, Materials Lifts, Manual and Electric
- Genie and Counterbalance Materials Lifters
- Scissor Lift Tables
- Drum Handling Equipment
- Crane Forks
- Load Weighing Equipment - Load Cells
- Tool Spring Balancers / Load Balancers
- Platform Trucks & Trolleys
-
Forklift Truck Attachment
- Fork Mounted Man Riding Baskets
- Environment & Waste Handling Attachments
- Fork Lift Truck Mounted Drum Handling Attachments
- Fork Mounted Jib and Hook Attachments
- Fork Truck Booms & Tines
- Stainless Steel Forklift Attachments
- Forklift Truck Fork Extensions
- Multi Fork Attachments
- Fork Truck Scoop Attachments
- Big Bag Fork Truck Attachment
- Closed Base Coil Support Attachments
- Forklift Fork Protection Sleeves
- Snow Plough Fork Lift Truck Attachments
- Other Forklift Truck & Telehandler Attachments
- Specialist Lifting Equipment
- Access and Safety Related
- Workshop and Shop Floor
- Screwjacks & Actuators
-
Height Safety
Height Safety Equipment
-
Fall Arrest and Height Safety Harnesses
- General Use Harnesses EN361
- Work Positioning Harnesses EN361 & EN358
- Rope Access Harnesses
- Rescue Harnesses EN1497 & EN361
- Ladies & Childrens Harnesses
- Hi Vis Jacket/Vest Harnesses
- Welders Harnesses
- ATEX (Anti-Static) Harnesses
- Linesman Harnesses
- Oil Derrick Harnesses
- Sport Climbing Harnesses
- Tree Surgeon Positioning Harnesses
- Sit and Chest Harnesses. EN361 EN356 & EN831
- Work Positioning & Restraint Belts EN358
- Fall Arrest, Restraint and Positioning Lanyards
- Height Safety and Fall Arrest Kits
- Inertia Reels and Retrieval Blocks
-
Confined Space and Rescue Systems
- Xtirpa Confined Space Davit Arm Systems and Components
- Sala Advanced Davit Arm Systems and Components
- Genesi Confined Space Systems
- Abtech Man-riding, Fall Arrest and Rescue Davits and Components
- Man-riding Hoists & Rescue Winches
- Fall Arrest & Rescue Tripods
- Fall Arrest Davit Arms & Posts for Working at Height
-
Fall Arrest & Man-riding Systems
- Manriding Systems, Baskets and Chairs
- Mobile Fall Arrest Gantries, Systems & Steps
- Rope Guided Fall Arresters (Steel & Synthetic Rope)
- Temporary Horizontal Fall Arrest Lifelines
- Vertical Fall Arrest Systems Permanently Installed
- Horizontal Fall Arrest Systems Permanently Installed
- Manriding Baskets Fork Truck and Overhead Crane
- Tank Side Entry and Vehicle Fall Arrest Systems
- Suspension Seats / Bosuns Chair Working at Height
- Collective Fall Arrest Systems
- Man-Riding Sheave Blocks
- Anchorage Devices
- Karabiners & Connectors
- Rescue, Evacuation & Rope Access
-
General Height Safety Gear
- Height Safety Accessories
- Industrial & Climbing Height Safety Helmets
- Synthetic Height Safety Rope & Anchorage Lines
- Height safety Pulley Wheels For Synthetic & Steel Wire Rope
- Black Height Safety Equipment & PPE
- Hot Work Equipment. Cutting, Grinding & Welding
- Cases, Bags, Backpacks, Holdalls. Height Safety Gear
- Telescopic Extension Pole for Height Safety Applications
- Wind Energy Height Safety Equipment
- Stainless Steel Fall Arrest Equipment
-
Fall Arrest and Height Safety Harnesses
- Home
- About Us
-
Contact
Get In Touch
- Home/
- Lifting Equipment/
- Screwjacks, Linear Actuators, Rotary Unions and ACME Ball Screws and Nuts/
- Duff Norton Screwjacks/
- Anti Backlash Machine Screwjack Actuator, 0.25t to 150t
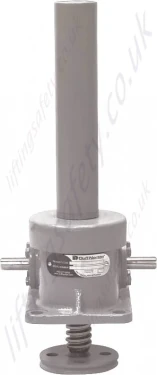
Anti Backlash Machine Screwjack Actuator, 0.25t to 150t
Anti-backlash screwjack actuator.
ABMS-4051
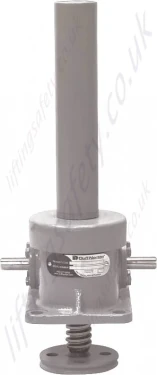
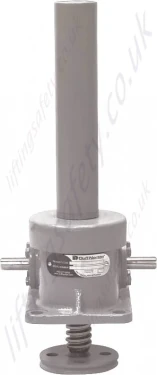
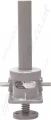
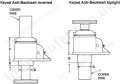
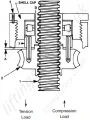
Anti Backlash Control
Even the best manufacturing processes produce clearances between a screw and a mating nut.
In applications where loads may be in either direction, backlash can result from these clearances creating unacceptable movement in the controlled mechanism as loads change.
These applications are common in the paper, plastic, film, sheet metal forming processes, satellite, or other load-reversing applications, such applications may be subjected to extreme vibrations.
These vibrations can produce constant movement between the screw and lifting nut which can hammer the threads and cause premature wear.
To reduce this screw-to-nut backlash to an absolute minimum, Anti-Backlash actuators were developed.
The design allows the backlash to be adjusted to the minimum value practical. As wear occurs, the actuator can be easily adjusted, without any disassembly, to return the backlash to its original minimum value.
Key Adaptor Dimensions for Anti-Backlash Actuators
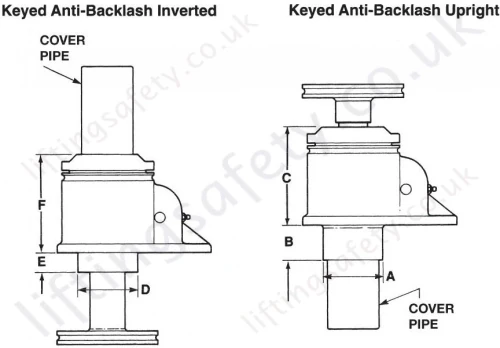
Actuator Capacity (tons) | Upright A Dia. (in) | Upright B (in) | Upright C (in) | Inverted D Dia. (in) | Inverted E (in) | Inverted F (in) |
1/4 & 1/2 | 1.66 | Pipe Length | 2.38 | 1.25 | .81 | 2.88 |
1 | 1.66 | .75 | 3.84 | 1.50 | .38 | 3.38 |
2 | 2.25 | 1.25 | 3.88 | 2.25 | .63 | 3.88 |
3 | 2.25 | 1.25 | 4.34 | 2.25 | .63 | 4.34 |
5 | 2.75 | 1.75 | 5.44 | 2.75 | .88 | 5.44 |
10 | 3.38 | 2.00 | 5.75 | 3.38 | 1.13 | 5.75 |
15 | 3.63 | 2.00 | 6.13 | 3.63 | 1.25 | 6.13 |
20 | 4.00 | 1.50 | 7.75 | 4.00 | 1.00 | 7.75 |
25 | 5.50 | 2.25 | 9.69 | 5.50 | 1.25 | 9.69 |
35 | 6.50 | 2.38 | 9.44 | 6.50 | 1.25 | 9.44 |
50 | 7.00 | 3.00 | 11.75 | 7.00 | 3.00 | 11.75 |
Anti-Backlash Machine Screw Actuators Performance Specifications
Capacity (tons) | 1/4 | 1/2 | 1 | 2 | 3 | 5 | 10 | 15 | 20 | 25 | 35 | 50 | 75 | 100 | 150 | |
Max. Speed Cface Driven (in/min)** | - | - | - | 72.0 | 72.0 | 108.0 | 108.0 | 108.0 | 108.0 | 107.5 | 107.5 | - | - | - | - | |
Max. Speed Red. Driven (in/Min)** | - | - | - | 14.4 | 14.14 | 21.9 | 21.9 | 21.9 | 21.9 | 22.2 | 22.4 | 12.2 | - | - | - | |
Lifting Screw | Diameter (in) | 1/2 | 5/8 | 3/4 | 1 | 1 | 1 1/2 | 2 | 2 1/4 | 2 1/2 | 3 | 3 3/4 | 4 1/2 | 5 | 6 | 7 |
Pitch (in) | 0.250 | 0.125 | 0.200 | 0.250 | 0.250 | 0.375 | 0.500 | 0.500 | 0.500 | 0.66 | 0.66 | 0.66 | 0.66 | 0.750 | 1.000 | |
Type | ACME | ACME | ACME | ACME | ACME | ACME | ACME | ACME | ACME | ACME | ACME | Mod.Sq. | Mod.Sq. | Mod.Sq. | Mod.Sq. | |
Worm Gear Ratios | Standard | 5:1 | 5:1 | 5:1 | 6:1 | 6:1 | 6:1 | 8:1 | 8:1 | 8:1 |
10 2/3:1 | 10 2/3:1 | 10 2/3:1 | 10 2/3:1 | 12:1 | 12:1 |
Optional Number 1 | - | - | 20:1 | 24:1 | 24:1 | 24:1 | 24:1 | 24:1 | 24:1 | 32:1 | 32:1 | 32:1 | 36:1 | 36:1 | 36:1 | |
Optional Number 2 | - | - | - | 12:1 | 12:1 | 12:1 | - | - | - | - | - | - | - | - | - | |
Turns of Worm for 1" Stroke | Standard | 20 | 40 | 25 | 24 | 24 | 16 | 16 | 16 | 16 | 16 | 16 | 16 | 16 | 16 | 12 |
Optional Number 1 | - | - | 100 | 96 | 96 | 64 | 48 | 48 | 48 | 48 | 48 | 48 | 48 | 48 | 36 | |
Optional Number 2 | - | - | - | 48 | 48 | 32 | - | - | - | - | - | - | - | - | - | |
Worm Torque and No Load (in-lb) | Standard | 2 | 2 | 5 | 5 | 5 | 10 | 20 | 20 | 30 | 40 | 50 | 100 | 150 | 200 | 250 |
Optional Number 1 | - | - | 5 | 5 | 5 | 10 | 20 | 20 | 30 | 40 | 50 | 100 | 150 | 200 | 250 | |
Optional Number 2 | - | - | 5 | 5 | 10 | - | - | - | - | - | - | - | - | - | - | |
Maximum Horsepower per Actuator | Standard | 1/3 | 1/3 | 1/2 | 2 | 2 | 4 | 5 | 5 | 5 | 8 | 8 | 15 | 15 | 25 | 25 |
Optional Number 1 | - | - | 1/4 | 1/2 | 3/4 | 3/4 | 1 1/2 | 1 1/2 | 1 1/2 | 2 1/2 | 2 1/2 | 6 | 6 | 11 | 11 | |
Optional Number 2 | - | - | - | 3/4 | 1 1/4 | 2 | - | - | - | - | - | - | - | - | - | |
Worm Torque Power at Full Load (in-lb) | Standard | 14 | 23 | 61 | 132 | 181 | 495 | 825 | 1573 | 2255 | 2970 | 4400 | 8250 | 13200 | 17600 | 30921 |
Optional Number 1 | - | - | 28 | 55 | 82 | 204 | 440 | 902 | 1287 | 1870 | 2640 | 4620 | 7095 | 9460 | 17050 | |
Optional Number 2 | - | - | - | 82 | 115 | 303 | - | - | - | - | - | - | - | - | - | |
Efficiency Rating (%) | Standard | 27.8 | 17.2 | 21.0 | 20.1 | 22.0 | 20.1 | 24.1 | 19.0 | 17.6 | 16.7 | 15.8 | 12.1 | 11.3 | 11.3 | 12.9 |
Optional Number 1 | - | - | 11.6 | 12.1 | 12.1 | 12.2 | 15.1 | 11.0 | 10.3 | 8.9 | 8.8 | 7.2 | 7.0 | 7.0 | 7.8 | |
Optional Number 2 | - | - | - | 16.1 | 17.2 | 16.4 | - | - | - | - | - | - | - | - | - | |
Weight with 6" Stroke (raise) (lb) | 2.3 | 2.3 | 5 | 17 | 17 | 35 | 52 | 66 | 93 | 160 | 240 | 410 | 1200 | 1200 | 1350 | |
Weight per Additional 1" Stroke (raise) (lb) | 0.1 | 0.1 | 0.3 | 0.3 | 0.3 | 0.9 | 1.4 | 1.5 | 2.6 | 2.5 | 3.7 | 5.5 | 9.0 | 9.0 | 12.6 | |
Key Torque (in-lb) | 40 | 70 | 175 | 460 | 670 | 1750 | 4700 | 7580 | 10625 | 14000 | 26500 | 47110 | 88650 | 118200 | 216000 | |
Max Worm Speed at Full Load (rpm) | Standard | 1469 | 909 | 521 | 955 | 696 | 509 | 382 | 200 | 140 | 170 | 115 | 115 | 72 | 90 | 51 |
Optional Number 1 | - | - | 573 | 573 | 573 | 232 | 215 | 105 | 73 | 84 | 60 | 82 | 53 | 73 | 41 | |
Optional Number 2 | - | - | - | 573 | 682 | 416 | - | - | - | - | - | - | - | - | - | |
Max Load at Full Horsepower and 1750 rpm (lb) | Standard | 407 | 474 | 469 | 2112 | 2285 | 2764 | 3978 | 3092 | 2698 | 4234 | 3832 | 5402 | 4485 | 8050 | 6361 |
Optional Number 1 | - | - | 356 | 1041 | 1705 | 879 | 1620 | 1157 | 764 | 1367 | 1082 | 2568 | 1427 | 4237 | 2610 | |
Optional Number 2 | - | - | - | 1136 | 2174 | 2119 | - | - | - | - | - | - | - | - | - |
Stainless Steel Anti-Backlash Actuators Performance Specifications
Capacity (tons) - 17-4PH Worm | 2 | 5 | 10 | 15 | 20 | 25 | 35 | 50 | 100 | |
Capacity (tons) - 316 SS Worm | 0.67 | 1.66 | 3.33 | 5.00 | 6.66 | 8.33 | 11.66 | 16.66 | 33.33 | |
Lifting Screw | Diameter (in) | 1 |
1 1/2 |
2 |
2 1/4 |
2 1/2 |
3 |
3 3/4 |
4 1/2 |
6 |
Pitch (in) | 0.250 |
0.375 |
0.500 |
0.500 |
0.500 |
0.666 |
0.666 |
0.666 |
0.750 |
|
Type | ACME | ACME |
ACME |
ACME |
ACME |
ACME |
ACME |
Mod.Sq. |
Mod.Sq. |
|
Worm Gear Ratios | Standard | 6:1 | 6:1 |
8:1 |
8:1 |
8:1 |
10 2/3:1 |
10 2/3:1 | 10 2/3:1 | 12:1 |
Optional Number 1 | 24:1 |
24:1 |
24:1 |
24:1 |
24:1 |
32:1 |
32:1 |
32:1 |
36:1 |
|
Optional Number 2 | 12:1 | 12:1 |
- |
- |
- |
- |
- |
- |
- |
|
Turns of Worm for 1" Raise | Standard | 24 | 16 |
16 | 16 |
16 | 16 |
16 | 16 | 16 |
Optional Number 1 | 96 | 64 | 48 |
48 |
48 |
48 |
48 |
48 |
48 |
|
Optional Number 2 | 48 | 32 |
- |
- |
- |
- |
- |
- |
- |
|
Worm Torque at No Load (in-lb) | Standard | 5 |
10 |
20 |
20 |
30 |
40 |
50 |
100 |
200 |
Optional Number 1 | 5 | 10 |
20 |
20 |
30 |
40 |
50 |
100 |
200 |
|
Optional Number 2 | 5 | 10 |
- |
- |
- |
- |
- |
- |
- |
|
Maximum Horsepower per Actuator | Standard | 2 | 4 |
5 |
5 |
5 |
8 |
8 |
15 |
25 |
Optional Number 1 | 1/2 | 3/4 |
1 1/2 |
1 1/2 |
1 1/2 |
2 1/2 |
2 1/2 |
6 |
11 |
|
Optional Number 2 | 3/4 | 2 |
- |
- |
- |
- |
- |
- |
- |
|
Worm Torque at Full Load (in-lb) 17-4PH Worm | Standard | 120 | 450 |
750 |
1430 |
2050 |
2700 |
4000 |
7500 |
16000 |
Optional Number 1 | 50 | 185 |
400 |
820 |
1170 |
1700 |
2400 |
4200 |
8600 |
|
Optional Number 2 | 75 | 275 |
- |
- |
- |
- |
- |
- |
- |
|
Worm Torque at Full Load (in-lb) 316SS Worm | Standard | 43 | 156 | 263 | 490 | 703 | 926 |
1366 |
2566 |
5466 |
Optional Number 1 | 20 | 68 |
147 |
287 |
410 |
593 |
833 |
1466 |
3000 |
|
Optional Number 2 | 28 |
98 |
- |
- |
- |
- |
- |
- |
- | |
Efficiency Rating (%) | Standard | 20.4 | 21.2 | 25.2 | 20.3 | 18.9 | 17.9 |
17.0 |
12.9 |
12.1 |
Optional Number 1 | 11.1 |
12.1 |
15.1 |
11.6 |
10.8 |
9.3 | 9.3 |
7.5 |
7.4 |
|
Optional Number 2 | 15.6 | 16.8 | - |
- |
- |
- |
- |
- |
- |
|
Weight with 6" Raise (lb) | 17 | 35 | 52 | 66 | 93 | 160 | 240 |
410 |
1200 |
|
Weight per Additional 1" Raise (lb) | 0.3 | 0.9 | 1.4 | 1.5 | 2.6 | 2.5 |
3.7 |
5.5 |
9.0 |
|
Key Torque (in-lb) | 153 |
581 |
1565 |
2527 |
3538 |
4665 |
8828 |
15697 |
39396 |
|
Max Worm Speed at Full Load (rpm) | Standard | 1750 | 1615 |
1198 |
643 |
449 |
544 |
369 |
368 |
288 |
Optional Number 1 | 1576 | 694 | 645 |
330 |
231 |
266 |
189 |
258 |
231 |
|
Optional Number 2 | 1669 | 1286 |
- |
- |
- |
- |
- |
- |
- |
|
Max Load at Full Horsepower and 1750 rpm (lb) | Standard | 1333 | 3047 |
4386 |
3406 |
2972 |
4664 |
4220 |
5949 |
8865 |
Optional Number 1 | 1156 | 972 |
1791 |
1276 |
843 |
1507 |
1192 |
2831 |
4671 |
|
Optional Number 2 | 1258 | 2339 | - |
- | - | - | - | - | - |
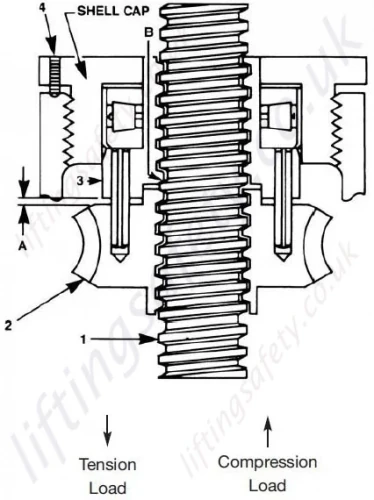
How it Works
When the screw (1) is under a compression load, the bottom of its thread surfaces are supported by the top thread surfaces of the worm gear (2). The anti-backlash nut (3), being pinned to the worm gear and floating on these pins and being adjusted downwards by the shell cap, forcing its bottom thread surfaces against the upper thread surfaces of the lifting screw at point (B).Thus backlash between the worm gear threadsand the lifting screw threads is reduced to a regulated minimum.
When wear occurs in the worm gear threads and the anti-backlash nut thread, the load carrting thickness of the worm gear thread will be reduced. This wear will create a gap at point (B) and provide backlash equal to the wear on the threads.
Under a compression load, the lifting screw will no longer be in contact with the lower thread surface of the anti-backlash nut. Under this condition, backlash will be present when a tension load is applied. The anti backlash feature can be maintained simply by adjusting the shell cap until the desired amount of backlash reduction is achieved. This will reduce the separation (A) between the anti- backlash nut and the worm gear and will reduce the backlash between the worm gear threads and the lifting screw to the desired minimum value.
To avoid binding and excessive wear, do not adjust lifting screw backlash to less than .0005".
When separation (A) has been reduced to zero, the wear limit has been reached.
Replace the worn gear and backlash nut set at this point.
This feature acts as a built in safety device.
Anti Backlash Control
Even the best manufacturing processes produce clearances between a screw and a mating nut.
In applications where loads may be in either direction, backlash can result from these clearances creating unacceptable movement in the controlled mechanism as loads change.
These applications are common in the paper, plastic, film, sheet metal forming processes, satellite, or other load-reversing applications, such applications may be subjected to extreme vibrations.
These vibrations can produce constant movement between the screw and lifting nut which can hammer the threads and cause premature wear.
To reduce this screw-to-nut backlash to an absolute minimum, Anti-Backlash actuators were developed.
The design allows the backlash to be adjusted to the minimum value practical. As wear occurs, the actuator can be easily adjusted, without any disassembly, to return the backlash to its original minimum value.
Key Adaptor Dimensions for Anti-Backlash Actuators
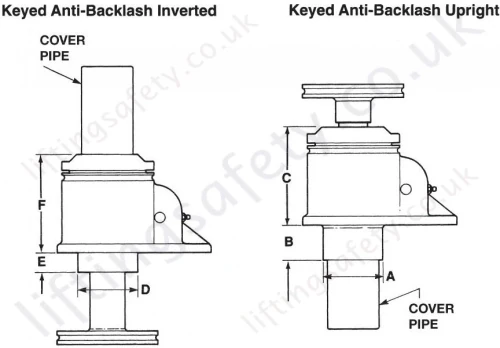
Actuator Capacity (tons) | Upright A Dia. (in) | Upright B (in) | Upright C (in) | Inverted D Dia. (in) | Inverted E (in) | Inverted F (in) |
1/4 & 1/2 | 1.66 | Pipe Length | 2.38 | 1.25 | .81 | 2.88 |
1 | 1.66 | .75 | 3.84 | 1.50 | .38 | 3.38 |
2 | 2.25 | 1.25 | 3.88 | 2.25 | .63 | 3.88 |
3 | 2.25 | 1.25 | 4.34 | 2.25 | .63 | 4.34 |
5 | 2.75 | 1.75 | 5.44 | 2.75 | .88 | 5.44 |
10 | 3.38 | 2.00 | 5.75 | 3.38 | 1.13 | 5.75 |
15 | 3.63 | 2.00 | 6.13 | 3.63 | 1.25 | 6.13 |
20 | 4.00 | 1.50 | 7.75 | 4.00 | 1.00 | 7.75 |
25 | 5.50 | 2.25 | 9.69 | 5.50 | 1.25 | 9.69 |
35 | 6.50 | 2.38 | 9.44 | 6.50 | 1.25 | 9.44 |
50 | 7.00 | 3.00 | 11.75 | 7.00 | 3.00 | 11.75 |
Anti-Backlash Machine Screw Actuators Performance Specifications
Capacity (tons) | 1/4 | 1/2 | 1 | 2 | 3 | 5 | 10 | 15 | 20 | 25 | 35 | 50 | 75 | 100 | 150 | |
Max. Speed Cface Driven (in/min)** | - | - | - | 72.0 | 72.0 | 108.0 | 108.0 | 108.0 | 108.0 | 107.5 | 107.5 | - | - | - | - | |
Max. Speed Red. Driven (in/Min)** | - | - | - | 14.4 | 14.14 | 21.9 | 21.9 | 21.9 | 21.9 | 22.2 | 22.4 | 12.2 | - | - | - | |
Lifting Screw | Diameter (in) | 1/2 | 5/8 | 3/4 | 1 | 1 | 1 1/2 | 2 | 2 1/4 | 2 1/2 | 3 | 3 3/4 | 4 1/2 | 5 | 6 | 7 |
Pitch (in) | 0.250 | 0.125 | 0.200 | 0.250 | 0.250 | 0.375 | 0.500 | 0.500 | 0.500 | 0.66 | 0.66 | 0.66 | 0.66 | 0.750 | 1.000 | |
Type | ACME | ACME | ACME | ACME | ACME | ACME | ACME | ACME | ACME | ACME | ACME | Mod.Sq. | Mod.Sq. | Mod.Sq. | Mod.Sq. | |
Worm Gear Ratios | Standard | 5:1 | 5:1 | 5:1 | 6:1 | 6:1 | 6:1 | 8:1 | 8:1 | 8:1 |
10 2/3:1 | 10 2/3:1 | 10 2/3:1 | 10 2/3:1 | 12:1 | 12:1 |
Optional Number 1 | - | - | 20:1 | 24:1 | 24:1 | 24:1 | 24:1 | 24:1 | 24:1 | 32:1 | 32:1 | 32:1 | 36:1 | 36:1 | 36:1 | |
Optional Number 2 | - | - | - | 12:1 | 12:1 | 12:1 | - | - | - | - | - | - | - | - | - | |
Turns of Worm for 1" Stroke | Standard | 20 | 40 | 25 | 24 | 24 | 16 | 16 | 16 | 16 | 16 | 16 | 16 | 16 | 16 | 12 |
Optional Number 1 | - | - | 100 | 96 | 96 | 64 | 48 | 48 | 48 | 48 | 48 | 48 | 48 | 48 | 36 | |
Optional Number 2 | - | - | - | 48 | 48 | 32 | - | - | - | - | - | - | - | - | - | |
Worm Torque and No Load (in-lb) | Standard | 2 | 2 | 5 | 5 | 5 | 10 | 20 | 20 | 30 | 40 | 50 | 100 | 150 | 200 | 250 |
Optional Number 1 | - | - | 5 | 5 | 5 | 10 | 20 | 20 | 30 | 40 | 50 | 100 | 150 | 200 | 250 | |
Optional Number 2 | - | - | 5 | 5 | 10 | - | - | - | - | - | - | - | - | - | - | |
Maximum Horsepower per Actuator | Standard | 1/3 | 1/3 | 1/2 | 2 | 2 | 4 | 5 | 5 | 5 | 8 | 8 | 15 | 15 | 25 | 25 |
Optional Number 1 | - | - | 1/4 | 1/2 | 3/4 | 3/4 | 1 1/2 | 1 1/2 | 1 1/2 | 2 1/2 | 2 1/2 | 6 | 6 | 11 | 11 | |
Optional Number 2 | - | - | - | 3/4 | 1 1/4 | 2 | - | - | - | - | - | - | - | - | - | |
Worm Torque Power at Full Load (in-lb) | Standard | 14 | 23 | 61 | 132 | 181 | 495 | 825 | 1573 | 2255 | 2970 | 4400 | 8250 | 13200 | 17600 | 30921 |
Optional Number 1 | - | - | 28 | 55 | 82 | 204 | 440 | 902 | 1287 | 1870 | 2640 | 4620 | 7095 | 9460 | 17050 | |
Optional Number 2 | - | - | - | 82 | 115 | 303 | - | - | - | - | - | - | - | - | - | |
Efficiency Rating (%) | Standard | 27.8 | 17.2 | 21.0 | 20.1 | 22.0 | 20.1 | 24.1 | 19.0 | 17.6 | 16.7 | 15.8 | 12.1 | 11.3 | 11.3 | 12.9 |
Optional Number 1 | - | - | 11.6 | 12.1 | 12.1 | 12.2 | 15.1 | 11.0 | 10.3 | 8.9 | 8.8 | 7.2 | 7.0 | 7.0 | 7.8 | |
Optional Number 2 | - | - | - | 16.1 | 17.2 | 16.4 | - | - | - | - | - | - | - | - | - | |
Weight with 6" Stroke (raise) (lb) | 2.3 | 2.3 | 5 | 17 | 17 | 35 | 52 | 66 | 93 | 160 | 240 | 410 | 1200 | 1200 | 1350 | |
Weight per Additional 1" Stroke (raise) (lb) | 0.1 | 0.1 | 0.3 | 0.3 | 0.3 | 0.9 | 1.4 | 1.5 | 2.6 | 2.5 | 3.7 | 5.5 | 9.0 | 9.0 | 12.6 | |
Key Torque (in-lb) | 40 | 70 | 175 | 460 | 670 | 1750 | 4700 | 7580 | 10625 | 14000 | 26500 | 47110 | 88650 | 118200 | 216000 | |
Max Worm Speed at Full Load (rpm) | Standard | 1469 | 909 | 521 | 955 | 696 | 509 | 382 | 200 | 140 | 170 | 115 | 115 | 72 | 90 | 51 |
Optional Number 1 | - | - | 573 | 573 | 573 | 232 | 215 | 105 | 73 | 84 | 60 | 82 | 53 | 73 | 41 | |
Optional Number 2 | - | - | - | 573 | 682 | 416 | - | - | - | - | - | - | - | - | - | |
Max Load at Full Horsepower and 1750 rpm (lb) | Standard | 407 | 474 | 469 | 2112 | 2285 | 2764 | 3978 | 3092 | 2698 | 4234 | 3832 | 5402 | 4485 | 8050 | 6361 |
Optional Number 1 | - | - | 356 | 1041 | 1705 | 879 | 1620 | 1157 | 764 | 1367 | 1082 | 2568 | 1427 | 4237 | 2610 | |
Optional Number 2 | - | - | - | 1136 | 2174 | 2119 | - | - | - | - | - | - | - | - | - |
Stainless Steel Anti-Backlash Actuators Performance Specifications
Capacity (tons) - 17-4PH Worm | 2 | 5 | 10 | 15 | 20 | 25 | 35 | 50 | 100 | |
Capacity (tons) - 316 SS Worm | 0.67 | 1.66 | 3.33 | 5.00 | 6.66 | 8.33 | 11.66 | 16.66 | 33.33 | |
Lifting Screw | Diameter (in) | 1 |
1 1/2 |
2 |
2 1/4 |
2 1/2 |
3 |
3 3/4 |
4 1/2 |
6 |
Pitch (in) | 0.250 |
0.375 |
0.500 |
0.500 |
0.500 |
0.666 |
0.666 |
0.666 |
0.750 |
|
Type | ACME | ACME |
ACME |
ACME |
ACME |
ACME |
ACME |
Mod.Sq. |
Mod.Sq. |
|
Worm Gear Ratios | Standard | 6:1 | 6:1 |
8:1 |
8:1 |
8:1 |
10 2/3:1 |
10 2/3:1 | 10 2/3:1 | 12:1 |
Optional Number 1 | 24:1 |
24:1 |
24:1 |
24:1 |
24:1 |
32:1 |
32:1 |
32:1 |
36:1 |
|
Optional Number 2 | 12:1 | 12:1 |
- |
- |
- |
- |
- |
- |
- |
|
Turns of Worm for 1" Raise | Standard | 24 | 16 |
16 | 16 |
16 | 16 |
16 | 16 | 16 |
Optional Number 1 | 96 | 64 | 48 |
48 |
48 |
48 |
48 |
48 |
48 |
|
Optional Number 2 | 48 | 32 |
- |
- |
- |
- |
- |
- |
- |
|
Worm Torque at No Load (in-lb) | Standard | 5 |
10 |
20 |
20 |
30 |
40 |
50 |
100 |
200 |
Optional Number 1 | 5 | 10 |
20 |
20 |
30 |
40 |
50 |
100 |
200 |
|
Optional Number 2 | 5 | 10 |
- |
- |
- |
- |
- |
- |
- |
|
Maximum Horsepower per Actuator | Standard | 2 | 4 |
5 |
5 |
5 |
8 |
8 |
15 |
25 |
Optional Number 1 | 1/2 | 3/4 |
1 1/2 |
1 1/2 |
1 1/2 |
2 1/2 |
2 1/2 |
6 |
11 |
|
Optional Number 2 | 3/4 | 2 |
- |
- |
- |
- |
- |
- |
- |
|
Worm Torque at Full Load (in-lb) 17-4PH Worm | Standard | 120 | 450 |
750 |
1430 |
2050 |
2700 |
4000 |
7500 |
16000 |
Optional Number 1 | 50 | 185 |
400 |
820 |
1170 |
1700 |
2400 |
4200 |
8600 |
|
Optional Number 2 | 75 | 275 |
- |
- |
- |
- |
- |
- |
- |
|
Worm Torque at Full Load (in-lb) 316SS Worm | Standard | 43 | 156 | 263 | 490 | 703 | 926 |
1366 |
2566 |
5466 |
Optional Number 1 | 20 | 68 |
147 |
287 |
410 |
593 |
833 |
1466 |
3000 |
|
Optional Number 2 | 28 |
98 |
- |
- |
- |
- |
- |
- |
- | |
Efficiency Rating (%) | Standard | 20.4 | 21.2 | 25.2 | 20.3 | 18.9 | 17.9 |
17.0 |
12.9 |
12.1 |
Optional Number 1 | 11.1 |
12.1 |
15.1 |
11.6 |
10.8 |
9.3 | 9.3 |
7.5 |
7.4 |
|
Optional Number 2 | 15.6 | 16.8 | - |
- |
- |
- |
- |
- |
- |
|
Weight with 6" Raise (lb) | 17 | 35 | 52 | 66 | 93 | 160 | 240 |
410 |
1200 |
|
Weight per Additional 1" Raise (lb) | 0.3 | 0.9 | 1.4 | 1.5 | 2.6 | 2.5 |
3.7 |
5.5 |
9.0 |
|
Key Torque (in-lb) | 153 |
581 |
1565 |
2527 |
3538 |
4665 |
8828 |
15697 |
39396 |
|
Max Worm Speed at Full Load (rpm) | Standard | 1750 | 1615 |
1198 |
643 |
449 |
544 |
369 |
368 |
288 |
Optional Number 1 | 1576 | 694 | 645 |
330 |
231 |
266 |
189 |
258 |
231 |
|
Optional Number 2 | 1669 | 1286 |
- |
- |
- |
- |
- |
- |
- |
|
Max Load at Full Horsepower and 1750 rpm (lb) | Standard | 1333 | 3047 |
4386 |
3406 |
2972 |
4664 |
4220 |
5949 |
8865 |
Optional Number 1 | 1156 | 972 |
1791 |
1276 |
843 |
1507 |
1192 |
2831 |
4671 |
|
Optional Number 2 | 1258 | 2339 | - |
- | - | - | - | - | - |
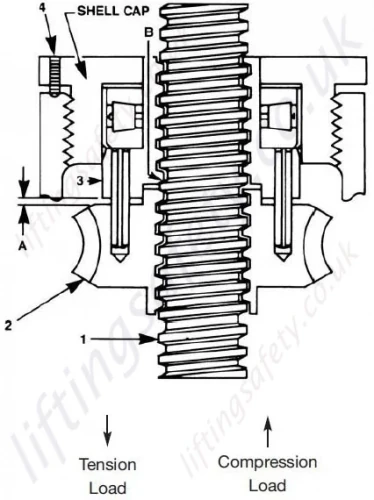
How it Works
When the screw (1) is under a compression load, the bottom of its thread surfaces are supported by the top thread surfaces of the worm gear (2). The anti-backlash nut (3), being pinned to the worm gear and floating on these pins and being adjusted downwards by the shell cap, forcing its bottom thread surfaces against the upper thread surfaces of the lifting screw at point (B).Thus backlash between the worm gear threadsand the lifting screw threads is reduced to a regulated minimum.
When wear occurs in the worm gear threads and the anti-backlash nut thread, the load carrting thickness of the worm gear thread will be reduced. This wear will create a gap at point (B) and provide backlash equal to the wear on the threads.
Under a compression load, the lifting screw will no longer be in contact with the lower thread surface of the anti-backlash nut. Under this condition, backlash will be present when a tension load is applied. The anti backlash feature can be maintained simply by adjusting the shell cap until the desired amount of backlash reduction is achieved. This will reduce the separation (A) between the anti- backlash nut and the worm gear and will reduce the backlash between the worm gear threads and the lifting screw to the desired minimum value.
To avoid binding and excessive wear, do not adjust lifting screw backlash to less than .0005".
When separation (A) has been reduced to zero, the wear limit has been reached.
Replace the worn gear and backlash nut set at this point.
This feature acts as a built in safety device.
You May Also Like
Contact Us About This Product
If you wish to receive a quote for this product, please use the tab above, this form is for general enquiries regarding this product only.
You can also Request a Quote using the Quote tab above!
You can easily add more than one item to the Quote Request. This is highly recommended as we will be able to suit your needs much more efficiently.