-
Lifting Equipment
Lifting Equipment
- Chain Hoists
-
Wire Rope Hoists & Winches
- Hand Operated Wire Rope Winches and Hoists
- Cable Pullers / Hoists, Wire Rope Manual Operation
- Electric Winches and Hoists, AC (Mains Powered)
- Scaffold Hoists & Accessories
- Overhead Wire Rope Crane Hoists
- Hydraulic Wire Rope Winches & Hoists
- Pneumatic Wire Rope Air Winches / Hoists (Lifting and Pulling)
- Vehicle Mounted Winches
- Tractel Wire Rope & Accessories
-
General Lifting Equipment
- Soft Lifting Slings
- Lifting Chain Slings
- Wire Rope Slings & Assemblies
- Lifting Shackles
- Eye Bolts and Nuts
- Weld-on Lifting Eyes and Lashing Points
- Lifting & Pulling Clamps
- Lifting Beams & Spreader Beams
- Precast Concrete Lifting
- Lifting Magnets, Permanent, Battery Electric and Manual
- Beam Trolleys and Crane Bridges, Push, Geared & Electric
- Equipment Identification Tags
-
Rigging Equipment
- Master Ring & Load Suspension Eyes
- Lifting & Rigging Hooks
- Turnbuckles & Rigging Screws
- Wire Rope Accessories and Fittings
- Snatch Blocks, Sheave Blocks and Crane Pulley Blocks
- Pulley Sheaves
- Lifting & Rigging Swivels - Eye, Hook & Shackle
- Load Restraint Equipment
- General Rigging Accessories
- Crosby Lifting & Rigging
-
Cranes & Gantry Systems
- Portable Davit Arms
- Swing Jib Cranes - Installed Floor & Wall Cranes
- Portable/Mobile Free-standing Swing Jib Cranes
- Aluminium Gantry Cranes
- Steel Gantry Cranes
- Fixed Steel Gantry Systems
- Shearlegs, Tripods & Quadpods
- Overhead Crane Systems
- Portable Shop-Floor/Workshop/Garage Cranes
- Counterbalance Floor, Workshop Cranes
- Scaffolding Runway Beam Systems
-
Material Handling & Jacking Equipment
- Machinery & Load Moving Skates
- Hydraulic Cylinders & Pumps
- Lifting Jacks
- Manhole Cover Lifters
- Hydraulic Pull Cylinders
- Hand Operated Pallet Trucks, Pump Trucks
- Stacker Trucks, Materials Lifts, Manual and Electric
- Genie and Counterbalance Materials Lifters
- Scissor Lift Tables
- Drum Handling Equipment
- Crane Forks
- Load Weighing Equipment - Load Cells
- Tool Spring Balancers / Load Balancers
- Platform Trucks & Trolleys
-
Forklift Truck Attachment
- Fork Mounted Man Riding Baskets
- Environment & Waste Handling Attachments
- Fork Lift Truck Mounted Drum Handling Attachments
- Fork Mounted Jib and Hook Attachments
- Fork Truck Booms & Tines
- Stainless Steel Forklift Attachments
- Forklift Truck Fork Extensions
- Multi Fork Attachments
- Fork Truck Scoop Attachments
- Big Bag Fork Truck Attachment
- Closed Base Coil Support Attachments
- Forklift Fork Protection Sleeves
- Snow Plough Fork Lift Truck Attachments
- Other Forklift Truck & Telehandler Attachments
- Specialist Lifting Equipment
- Access and Safety Related
- Workshop and Shop Floor
- Screwjacks & Actuators
-
Height Safety
Height Safety Equipment
-
Fall Arrest and Height Safety Harnesses
- General Use Harnesses EN361
- Work Positioning Harnesses EN361 & EN358
- Rope Access Harnesses
- Rescue Harnesses EN1497 & EN361
- Ladies & Childrens Harnesses
- Hi Vis Jacket/Vest Harnesses
- Welders Harnesses
- ATEX (Anti-Static) Harnesses
- Linesman Harnesses
- Oil Derrick Harnesses
- Sport Climbing Harnesses
- Tree Surgeon Positioning Harnesses
- Sit and Chest Harnesses. EN361 EN356 & EN831
- Work Positioning & Restraint Belts EN358
- Fall Arrest, Restraint and Positioning Lanyards
- Height Safety and Fall Arrest Kits
- Inertia Reels and Retrieval Blocks
-
Confined Space and Rescue Systems
- Xtirpa Confined Space Davit Arm Systems and Components
- Sala Advanced Davit Arm Systems and Components
- Genesi Confined Space Systems
- Abtech Man-riding, Fall Arrest and Rescue Davits and Components
- Man-riding Hoists & Rescue Winches
- Fall Arrest & Rescue Tripods
- Fall Arrest Davit Arms & Posts for Working at Height
-
Fall Arrest & Man-riding Systems
- Manriding Systems, Baskets and Chairs
- Mobile Fall Arrest Gantries, Systems & Steps
- Rope Guided Fall Arresters (Steel & Synthetic Rope)
- Temporary Horizontal Fall Arrest Lifelines
- Vertical Fall Arrest Systems Permanently Installed
- Horizontal Fall Arrest Systems Permanently Installed
- Manriding Baskets Fork Truck and Overhead Crane
- Tank Side Entry and Vehicle Fall Arrest Systems
- Suspension Seats / Bosuns Chair Working at Height
- Collective Fall Arrest Systems
- Man-Riding Sheave Blocks
- Anchorage Devices
- Karabiners & Connectors
- Rescue, Evacuation & Rope Access
-
General Height Safety Gear
- Height Safety Accessories
- Industrial & Climbing Height Safety Helmets
- Synthetic Height Safety Rope & Anchorage Lines
- Height safety Pulley Wheels For Synthetic & Steel Wire Rope
- Black Height Safety Equipment & PPE
- Hot Work Equipment. Cutting, Grinding & Welding
- Cases, Bags, Backpacks, Holdalls. Height Safety Gear
- Telescopic Extension Pole for Height Safety Applications
- Wind Energy Height Safety Equipment
- Stainless Steel Fall Arrest Equipment
-
Fall Arrest and Height Safety Harnesses
- Home
- About Us
-
Contact
Get In Touch
- Home/
- Lifting Equipment/
- General Industrial Lifting Equipment/
- Lifting Clamps (Lifting & Pulling Applications)/
- Remote Release and Drop Test Clamps/
- LiftingSafety "Load Release" Remote Hook-Clamp - Range 590kg to 70 tonne (Higher capacities available on request)
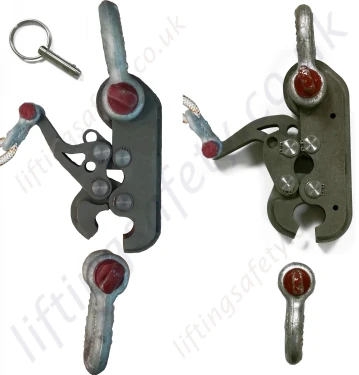
LiftingSafety "Load Release" Remote Hook-Clamp - Range 590kg to 70 tonne (Higher capacities available on request)
Manual, Hydraulic, Pneumatic operation, Stainless Steel Corrosion resistant SubSea Auto Remote Release Offshore Clamp. Shackles are not included as standard.
LARH-4193
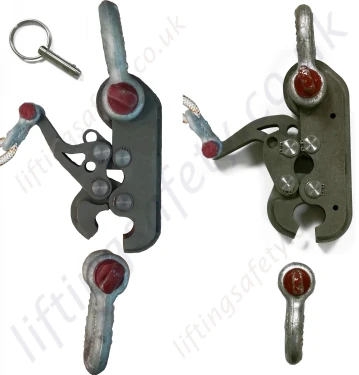
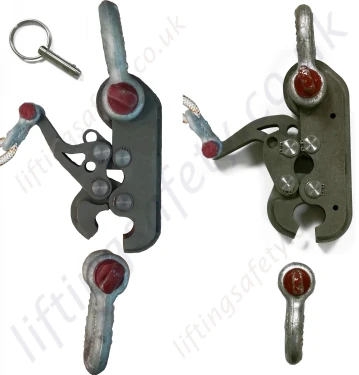
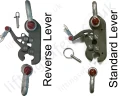
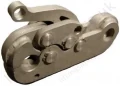
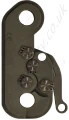
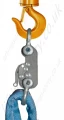
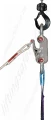
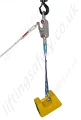
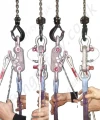
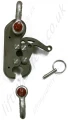
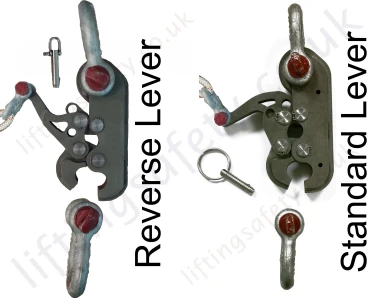
*Shackles not included - Available upon request.
LiftingSafety's Automatic release Hook-Clamps provide a unique method to Automatically release a load from the rigging and can easily be adapted to suit customers requirements. Fully corrosion resistant designed specifically for subsea and offshore use with a proven pedigree and reliability.
The LiftingSafety Automatic Load Release Hook-Clamp is perfect for when you need to quickly release a load, it comes in a large range of working capacities (safe working loads) and can be fabricated to suit your needs with bespoke capacities etc...
Examples of use
- To prevent the need to work at height, enabling the load to be disconnected from distance with-out the need to climb onto the load.
- As a direct alterative to hydraulic release shackles, suitable for deep-water subsea operations.
- Fully certified for use in the UK, Europe and the United states of America (USA), CE Marked and supplied with an EC Declaration of conformity / Operation and user manual.
- Used to precisely place a load in position then remotely (and therefore safely) release the load from the crane hook (rigging gear). Using this method the clamp releases the load when the weight has been transferred to the floor, (other surface for example lorry trailer building, ground etc....)
- The Auto HookClamp can also used as a drop test clamp or load dropping clamp. This is where the clamp is used to release the load "under load", for example when dropping sea defences into the sea from a boat.
- Off-shore applications as used by the oil, gas, maritime, coastal, fishing, lifeboat industries etc....
- Sub-Sea use, made completely from aerospace-grade stainless steel the HookClamp has the ultimate in corrosion resistance.
- Third part whiteness test and certification available at extra cost (3rd party approval DNV, BV, Lloyds etc...)
- Conversion for subsea ROV operation (Work class Remote operated vehicle also referred to as WROV usually by manipulator arm though also can be converted to hotstab.
- A multitude of general Industrial applications; indeed for any application where the rigging gear needs to be disconnected though is is an awkward, difficult to get to position. Automatic remote release of the rigging gear prevents unavoidable accidents.
- Ideal for use in the water utilities industry to automatically place pumps into sumps or wet wells.
- The manual release lever can be supplied pointing down (towards the opening jaw) for automatic release applications below ground; pulling up releases the load (known as a reverse lever). Alternatively the release lever / arm can be supplied pointing up (towards the rigging gear / anchorage eye) and this is used for automatic release applications where the operator is below the load. Both lever types can release the load when the operator is adjacent to the HookClamp.
- Back-up secondary safety hitch pin - The. manual release of the loaded Hook-Clamp can only be activated by first removing the safety / hitch pin. This is done either manually (directly by hand) or by a pull cord attached to the spring loaded safety hitch pin; ie, remotely and safety from a distance. The safety hitch pin release cord can be activated from any direction. Once the safety hitch pin has been removed the clamp is “loaded” or “Live” and pulling the cord attached to the release lever WILL DROP / RELEASE the load.
As standard the umbilical hose, hose reeler and power pack (HPU or pneumatic) supplied by the customer though we can quote to supply if requested.
Either end of the Hook-Clamp can be attached to a sling / shackle / hook allowing multiple uses, the load can then be released by use of a lanyard pulling the release lever or by using one of the remote-load release options available, see the 'Options' tab for more information. (manual, hydraulic, pneumatic, squib-fired thruster.)
General Specifications
- Fabricated by precision-cut computer-generated parts
- Load Release Lever can be inverted (Standard or reverse)
- Effort required to release the load can be adjusted to suit your application (effort can be reduced or increased)
- Made from aerospace-grade stainless steel (corrosion resistant)
- No Springs, reliable and robust design
- Multi-Directional operation, can be used in the horizontal or vertical plain. To place a load safely and precisely or as a dropping clamp.
- Low Friction resistance
- Safety Hitch Pin Safety Locking, manual or remotely spring loaded for remote activation (secondary safety back-up)
- Safe Release Under Load if required (Use as a dropping or drop test clamp)
- Safe working loads / Capacities range from 590kg to 69,000kg though special bespoke HookClamps are available on request, (we have designed and made units up to 250 tonne though greater capacities can be made on request)
- Special features are available on request
Video Examples
Reverse Lever - Manual (Pull) Release Pin
Reverse Lever - Spring Release Safety Pin
Manual Release - LS-Series (standard) |
|
![]() |
On the standard Hook-Clamp model, the lever is lifted to release the front clamp and allow the load to be released, it can be locked by a pin and ranges from 560kg to 69,000kg |
Manual Release S-Series (Steel Supporting Plate Only for Horizontal applications only) |
|
![]() |
The "S-Series" Hook-Clamp is affixed to a steel plate to allow more accuracy when attempting to release a load, applications such as towing and off-loading in the ocean are perfect for this Hook-Clamp |
Pneumatic / Compressed Air Release (Manual Release back-up) PNU-Series |
|
![]() |
The "PNU-Series" Hook-Clamp is fitted with a compressed air cylinder (Pneumatic ram) and allows for air pressure to release the load. The Air Cylinders operate at 60 to 100 PSI. |
Manual Release RL-Series (Inverted Release lever for activation/operation below the load) |
|
![]() |
The "RL Series" Hook-Clamp is simply a reversed lever. This can provide a better angle of load release in some cases. For example, this option would be needed when the operator needs to release the shackle/rigging gear when the load is positioned above the operator. |
Hydraulic Release (Manual Release back-up) HYDRA-Series |
|
![]() |
The "HYDRA Series" Hook-Clamp is fitted with a hydraulic cylinder mounted below the device, This setup can be used to replace a hydraulic release shackle (or hydraulic shackle). Above the cylinder is a plunger which penetrates through a hole in the body below the toggle pin. When this hydraulic system is activated, the cylinder pushes through the plunger and the toggle pin forcing the clamp to release the shackle (or other rigging gear). The hydraulic shackle release Hook-Clamp range can be operated remotely by a single 1/4" hydraulic hose. It can be operated by a manual hand pump, remote accumulator or power pack (HPU) Most commonly used for subsea/offshore applications for hydraulic release of shackles. |
General Information
- General Product Design Features - The load release device combes an old and proven four-point-toggle-linkage principle with computer-generated parts precision-cut by water jet from aerospace-grade stainless steel plate. These parts are welded together and movably connected by pivot pins to form the device. The Remote load release device can be used subsea or on dry land, for automatic releasing of a shackle to place a load safely with-out the need for the operator to manual disconnection from the slings. It can also be used as a drop test or dropping devise. (for example dropping coastal defences into the sea).
- Product Material / Specifications - All Remote load release device parts are longitudinally cut from aerospace-grade 15-5 PH stainless steel plate. Precipitation hardening stainless steels are chromium-nickel alloys. Pins are turned from 15-5 stainless steel round stock. All material is aircraft quality, grade XM-12 and meets the following specifications: AMS 5659, BMS 7-240, AMS 5862, and ASTM A564.
- Welding, Heat Treatment, and Lubrication - All welding is with 17-4 SS wire only. All welded parts and pins are thoroughly cleaned and heat treated to H-1025 which increases the rating of the welding by 20-30% and the parts by 15%. Heat treating also results in improved mechanical, fatigue and corrosion properties across the board. Final assembly of the product includes the light application of a lubricant to each pin such as AQUA Lube, to protect the pin surfaces from pitting during extended marine use and aid in smooth mechanical function of the device. For higher capacity units, an NLGI #2.5 grease with moly added and a temperature range from 0 to 425F is applied.
- Quality Control - The manufacturer assumes the responsibility of inspecting each production unit for function, specifications, and appearance. Units not meeting the above rigid requirements are rejected.
Warnings
- Improper use of the Remote load release device may cause injury.
- Hitch-pin must be used to totally prevent inadvertent release.
- Do not use the Remote load release device release line as a tag line or put any tension on it until time to release. An additional tag line secured to the upper shackle and kept taught at all times is highly recommended to maintain a slack release line and prevent load twisting.
- Stay clear of all objects released under load.
- Do not exceed load capacity of this device.
- Choose the proper size Remote load release device so that it is not loaded with or releasing more than its rated load.
- Do not side load the Remote load release device as it may cause loss of retainer rings and other parts or permanently damage the device.
- While in its loaded position, do not obstruct the Remote load release device so as to prevent its body being aligned straight with the line of load. Misalignment may prevent the movable jaw from releasing the connected member even with the device in the released position.
Maintenance
- Inspection of the Remote load release device is advised after each use.
- After use in or near sea water, a fresh water rinse of the Remote load release device is advised before it is stored.
- Pivot pins may require periodic re-lubrication.
Load Definitions
- Static Load: Forces solely due to the weight or gravity of objects being handled.
- Dynamic Load: A load created by motion of the object that increases or decreases the static load.
- Hydrodynamic Load: A load resulting from motion through the water including lift and drag.
- Inertial Load: A load resulting from accelerated releasing caused by tension on the object that is greater than gravity.
- Total Load: The sum of all above loads or forces acting on the object
Dimensions & Specifications
![]() |
|||||||||||
Part N° |
Recommended Shackle Size |
Dimensions (mm) | SWL (kg) | Break load (kg) | Weight (kg) | ||||||
Recommended shackle opening | Recommended shackle pin dia. | C | D | E | F | G | |||||
4193-T22955 | Keyring | -- | -- | 9.52 | 44.4 | -- | 4.76 | 31.75 | NOT RATED | 0.36 | |
4193-T22956 | 1/4" | 11.93 | 7.87 | 10.41 | 73.39 | 4.57 | 9.39 | 49.78 | 590 | 2,902 | 0.14 |
4193-T22957 | 7/16" | 19.05 | 12.7 | 17.52 | 114.3 | 6.35 | 13.97 | 79.5 | 1,450 | 7,529 | 0.58 |
4193-T22958 | 5/8" | 26.92 | 19.05 | 25.4 | 168.14 | 9.65 | 20.57 | 115.82 | 3,190 | 15,966 | 1.81 |
4193-T22959 | 3/4" | 31.75 | 22.09 | 30.22 | 195.07 | 10.92 | 23.62 | 140.46 | 4,330 | 21,708 | 2.85 |
4193-T22960 | 1" | 42.92 | 28.7 | 41.4 | 247.65 | 14.22 | 30.73 | 174.49 | 7,185 | 35,924 | 5.67 |
4193-T22961 | 1-3/8" | 57.15 | 38.1 | 53.84 | 334.01 | 19.05 | 41.4 | 232.41 | 12,700 | 63,502 | 14.5 |
4193-T22962 | 1-1/2" | 60.45 | 41.14 | 57.15 | 361.95 | 20.57 | 45.21 | 251.96 | 14,905 | 74,525 | 18.14 |
4193-T22963 | 1-3/4" | 73.15 | 50.8 | 69.85 | 446.02 | 25.4 | 54.86 | 310.13 | 22,770 | 113,851 | 31.2 |
4193-T22964 | 2" | 82.55 | 57.15 | 79.5 | 501.14 | 28.44 | 62.48 | 349.25 | 28,750 | 143,743 | 48.98 |
4193-T22965 | 2-1/2" | 104.9 | 69.85 | 98.55 | 612.9 | 34.79 | 76.45 | 426.97 | 42,970 | 214,866 | 89.35 |
4193-T22966 | 3" | 127 | 82.55 | 120.65 | 782.06 | 44.45 | 97.79 | 544.32 | 69,960 | 349,810 | 138.8 |
The Hook-Clamp consists of several moving parts that allow the 'jaw' to open and release a load, generally you would use a release line to attach to the lever, pull this line and the load will release.
Alternative Methods of Release
These are the alternative methods for releasing the shackle:
- Manually, pulling a long release line. No modification of the device is required. This method is used with lower capacity models, offers the lowest cost, and has many satisfied users.
- Hydraulically, using a winch and cable, such as used with a deck-mounted crane, to pay out the load against a secured release line. No modification of the device is required for this method.
- Hydraulically, paying out the load against a fixed-length, bulkhead-mounted release cable. Using a clevis instead of a shackle, a bulkhead-mounted hydraulic ram is attached to the rear end of the horizontally positioned devise to pull it back after the unit is locked. The release cable is then secured to the bulkhead and when release is desired, the hydraulic ram is actuated, allowing the Remote load release device to move toward the load and eventually against the secured release cable and the load releases the unit. This method allows the instalment of a pressure gauge into the hydraulic system to determine the actual tensile load being released. No modification of the device is required
- Explosive electric squib thrusters inserted into a special chamber below the toggle pin are used successfully to activate the device.
- Hydraulic pressure to drive a hydraulic cylinder to actuate the release lever of the Remote load release device is being used with the device ram models. These units can be activated by hydraulic hand pump, air-hydraulic foot pump, or electric pump.
- Air Cylinders provide another method of release and are fitted for activation using shop air at 60 to 100 PSI.
Device Locking
- Having secured the recommended shackle to the rear end of the Hook-Clamp (anchorage / top suspension eye), open the jaw by removing the hitch pin and lifting up the release lever and opening it to the released position. Insert the pin of the shackle to be released into the jaw opening.
- Secure the shackle by closing the release lever to the locked position and firmly lock the toggle pin over centre with a vice-grip-like snap.
- The shackle is now held firmly locked even with no load on the device. The safety pin (Hitch pin) can be reinserted to prevent inadvertent release.
- The Hook-Clamp is now ready to be loaded. Once the safety / hitch pin is removed, the Hook-Clamp is armed and ready to be released. Either to “set down” a load or to drop a load in a controlled manor (as a drop test / dropping clamp)
Device Releasing
Manual release of the loaded Hook-Clamp is activated by first removing the safety / hitch pin. This is done either manually (directly by hand) or by a pull cord attached to the spring loaded safety hitch pin; i.e. remotely and safety from a distance. The safety hitch pin release cord can be activated from any direction.
Once the safety hitch pin has been removed the clamp is “loaded” or “Live” and pulling the cord attached to the release lever WILL DROP / RELEASE the load. Pulling firmly on a release line connected to the end of the release lever also means that the operator can safety release the load away from the “danger area”. The release line can be activated “Directly” in any direction within the 90 degrees perpendicular and parallel to the line of load. The “Standard” release lever can also be operated from above the load as shown in the diagram below with the use of a suitable pulley; effectively giving 180 degree operation.
The Hook-Clamp can release the load with or without load on the unit. (providing the safety hitch pin is removed).
The use of the hitch pin is not required to secure the device in the locked position. It is an added, secondary safety measure preventing inadvertent release. A safety hitch pin is provided with each unit. The standard safety hitch pin is not spring loaded for remote operation (from distance by a pull cord).
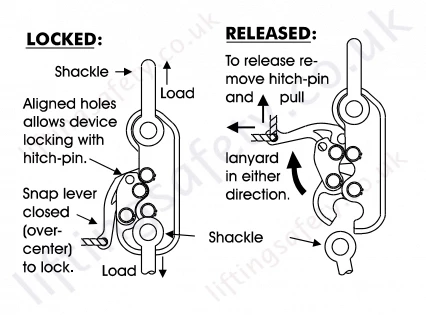
Capacities and Release Capacities.
Detailed below are the figures of the estimated effort required to release a load at full capacity. This effort can be adjusted by following the instructions below.
Safe Working Load | Estimated Effort To Pull Lanyard To Release Capacity Load (Can be adjusted, see below) |
590kg | 3.62kg |
1,507kg | 8.61kg |
3,194kg | 18.14kg |
4,342kg | 39.91kg |
7,186kg | 65.77kg |
12,776kg | 117kg |
14,902kg | 136.53kg |
22,770kg | 208kg |
28,747kg | 263kg |
42,975kg | 393kg |
69,960kg | 640kg |
Remote Load Release Device Hitch-Pin
The hitch pin can be supplied "Spring Loaded" remote triggered release. This means that the hitch pin can be remotely removed from the body of the Hook-Clamp by use a pull-cord attached to a spring loaded hitch pin and therefore ensuring an additional level of safety even when the operator cannot physically reach the hitch pin to physically release it!
Adjusting The Effort Required to Operate the Manual release lever (Remote load release device Over-Centre Pressure Adjustment)
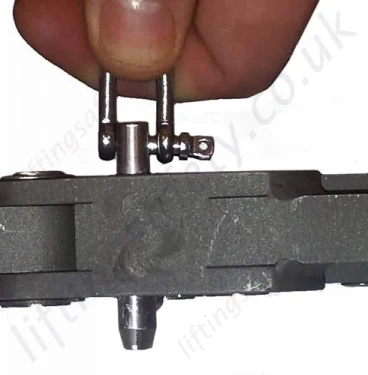
Standard Release Safety Pin Design
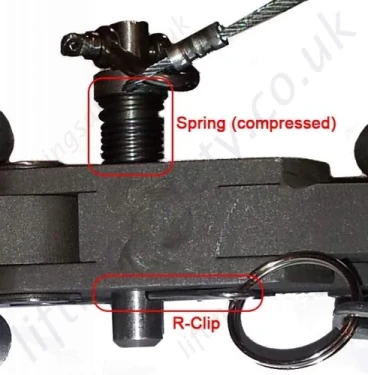
Spring Release Safety Pin R Clip Design
Ample material has been left at the tip of the movable jaw (see arrow) where the jaw and body come in contact. This aids in holding the device securely over-centre in the locked position even when no load is applied to the device. It also helps prevent inadvertent release of the device.
Should the user require that the effort to lock the release lever of the device over-centre be reduced, the procedure is to locate the area where the surface of the jaw comes in contact with the body and lightly file or grind off material in that area.
It is important to test the effort frequently after some material has been removed so as to prevent the removal of too much material.
Should the user require that the effort to lock the release lever of the device over-centre be increased, the procedure is to increase the thickness of the material between the two surfaces by applying a center punch mark in the area of the jaw where the surfaces meet. Should there still be insufficient material to ensure the positive locking integrity of the device, the contact area of the jaw will need to be spot-welded. This welded material will then need to be ground to the appropriate thickness.
Release Operation
Standard Release Lever | Reverse Release Lever | Standard Lever Release with Pulley (the same can be done with reverse lever if necessary) |
![]() |
![]() |
![]() |
Pricing
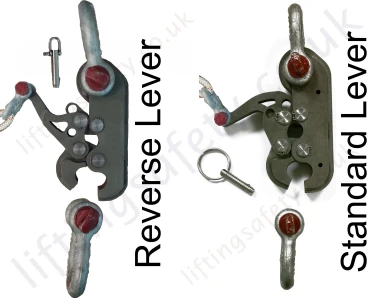
*Shackles not included - Available upon request.
LiftingSafety's Automatic release Hook-Clamps provide a unique method to Automatically release a load from the rigging and can easily be adapted to suit customers requirements. Fully corrosion resistant designed specifically for subsea and offshore use with a proven pedigree and reliability.
The LiftingSafety Automatic Load Release Hook-Clamp is perfect for when you need to quickly release a load, it comes in a large range of working capacities (safe working loads) and can be fabricated to suit your needs with bespoke capacities etc...
Examples of use
- To prevent the need to work at height, enabling the load to be disconnected from distance with-out the need to climb onto the load.
- As a direct alterative to hydraulic release shackles, suitable for deep-water subsea operations.
- Fully certified for use in the UK, Europe and the United states of America (USA), CE Marked and supplied with an EC Declaration of conformity / Operation and user manual.
- Used to precisely place a load in position then remotely (and therefore safely) release the load from the crane hook (rigging gear). Using this method the clamp releases the load when the weight has been transferred to the floor, (other surface for example lorry trailer building, ground etc....)
- The Auto HookClamp can also used as a drop test clamp or load dropping clamp. This is where the clamp is used to release the load "under load", for example when dropping sea defences into the sea from a boat.
- Off-shore applications as used by the oil, gas, maritime, coastal, fishing, lifeboat industries etc....
- Sub-Sea use, made completely from aerospace-grade stainless steel the HookClamp has the ultimate in corrosion resistance.
- Third part whiteness test and certification available at extra cost (3rd party approval DNV, BV, Lloyds etc...)
- Conversion for subsea ROV operation (Work class Remote operated vehicle also referred to as WROV usually by manipulator arm though also can be converted to hotstab.
- A multitude of general Industrial applications; indeed for any application where the rigging gear needs to be disconnected though is is an awkward, difficult to get to position. Automatic remote release of the rigging gear prevents unavoidable accidents.
- Ideal for use in the water utilities industry to automatically place pumps into sumps or wet wells.
- The manual release lever can be supplied pointing down (towards the opening jaw) for automatic release applications below ground; pulling up releases the load (known as a reverse lever). Alternatively the release lever / arm can be supplied pointing up (towards the rigging gear / anchorage eye) and this is used for automatic release applications where the operator is below the load. Both lever types can release the load when the operator is adjacent to the HookClamp.
- Back-up secondary safety hitch pin - The. manual release of the loaded Hook-Clamp can only be activated by first removing the safety / hitch pin. This is done either manually (directly by hand) or by a pull cord attached to the spring loaded safety hitch pin; ie, remotely and safety from a distance. The safety hitch pin release cord can be activated from any direction. Once the safety hitch pin has been removed the clamp is “loaded” or “Live” and pulling the cord attached to the release lever WILL DROP / RELEASE the load.
As standard the umbilical hose, hose reeler and power pack (HPU or pneumatic) supplied by the customer though we can quote to supply if requested.
Either end of the Hook-Clamp can be attached to a sling / shackle / hook allowing multiple uses, the load can then be released by use of a lanyard pulling the release lever or by using one of the remote-load release options available, see the 'Options' tab for more information. (manual, hydraulic, pneumatic, squib-fired thruster.)
General Specifications
- Fabricated by precision-cut computer-generated parts
- Load Release Lever can be inverted (Standard or reverse)
- Effort required to release the load can be adjusted to suit your application (effort can be reduced or increased)
- Made from aerospace-grade stainless steel (corrosion resistant)
- No Springs, reliable and robust design
- Multi-Directional operation, can be used in the horizontal or vertical plain. To place a load safely and precisely or as a dropping clamp.
- Low Friction resistance
- Safety Hitch Pin Safety Locking, manual or remotely spring loaded for remote activation (secondary safety back-up)
- Safe Release Under Load if required (Use as a dropping or drop test clamp)
- Safe working loads / Capacities range from 590kg to 69,000kg though special bespoke HookClamps are available on request, (we have designed and made units up to 250 tonne though greater capacities can be made on request)
- Special features are available on request
Video Examples
Reverse Lever - Manual (Pull) Release Pin
Reverse Lever - Spring Release Safety Pin
Manual Release - LS-Series (standard) |
|
![]() |
On the standard Hook-Clamp model, the lever is lifted to release the front clamp and allow the load to be released, it can be locked by a pin and ranges from 560kg to 69,000kg |
Manual Release S-Series (Steel Supporting Plate Only for Horizontal applications only) |
|
![]() |
The "S-Series" Hook-Clamp is affixed to a steel plate to allow more accuracy when attempting to release a load, applications such as towing and off-loading in the ocean are perfect for this Hook-Clamp |
Pneumatic / Compressed Air Release (Manual Release back-up) PNU-Series |
|
![]() |
The "PNU-Series" Hook-Clamp is fitted with a compressed air cylinder (Pneumatic ram) and allows for air pressure to release the load. The Air Cylinders operate at 60 to 100 PSI. |
Manual Release RL-Series (Inverted Release lever for activation/operation below the load) |
|
![]() |
The "RL Series" Hook-Clamp is simply a reversed lever. This can provide a better angle of load release in some cases. For example, this option would be needed when the operator needs to release the shackle/rigging gear when the load is positioned above the operator. |
Hydraulic Release (Manual Release back-up) HYDRA-Series |
|
![]() |
The "HYDRA Series" Hook-Clamp is fitted with a hydraulic cylinder mounted below the device, This setup can be used to replace a hydraulic release shackle (or hydraulic shackle). Above the cylinder is a plunger which penetrates through a hole in the body below the toggle pin. When this hydraulic system is activated, the cylinder pushes through the plunger and the toggle pin forcing the clamp to release the shackle (or other rigging gear). The hydraulic shackle release Hook-Clamp range can be operated remotely by a single 1/4" hydraulic hose. It can be operated by a manual hand pump, remote accumulator or power pack (HPU) Most commonly used for subsea/offshore applications for hydraulic release of shackles. |
General Information
- General Product Design Features - The load release device combes an old and proven four-point-toggle-linkage principle with computer-generated parts precision-cut by water jet from aerospace-grade stainless steel plate. These parts are welded together and movably connected by pivot pins to form the device. The Remote load release device can be used subsea or on dry land, for automatic releasing of a shackle to place a load safely with-out the need for the operator to manual disconnection from the slings. It can also be used as a drop test or dropping devise. (for example dropping coastal defences into the sea).
- Product Material / Specifications - All Remote load release device parts are longitudinally cut from aerospace-grade 15-5 PH stainless steel plate. Precipitation hardening stainless steels are chromium-nickel alloys. Pins are turned from 15-5 stainless steel round stock. All material is aircraft quality, grade XM-12 and meets the following specifications: AMS 5659, BMS 7-240, AMS 5862, and ASTM A564.
- Welding, Heat Treatment, and Lubrication - All welding is with 17-4 SS wire only. All welded parts and pins are thoroughly cleaned and heat treated to H-1025 which increases the rating of the welding by 20-30% and the parts by 15%. Heat treating also results in improved mechanical, fatigue and corrosion properties across the board. Final assembly of the product includes the light application of a lubricant to each pin such as AQUA Lube, to protect the pin surfaces from pitting during extended marine use and aid in smooth mechanical function of the device. For higher capacity units, an NLGI #2.5 grease with moly added and a temperature range from 0 to 425F is applied.
- Quality Control - The manufacturer assumes the responsibility of inspecting each production unit for function, specifications, and appearance. Units not meeting the above rigid requirements are rejected.
Warnings
- Improper use of the Remote load release device may cause injury.
- Hitch-pin must be used to totally prevent inadvertent release.
- Do not use the Remote load release device release line as a tag line or put any tension on it until time to release. An additional tag line secured to the upper shackle and kept taught at all times is highly recommended to maintain a slack release line and prevent load twisting.
- Stay clear of all objects released under load.
- Do not exceed load capacity of this device.
- Choose the proper size Remote load release device so that it is not loaded with or releasing more than its rated load.
- Do not side load the Remote load release device as it may cause loss of retainer rings and other parts or permanently damage the device.
- While in its loaded position, do not obstruct the Remote load release device so as to prevent its body being aligned straight with the line of load. Misalignment may prevent the movable jaw from releasing the connected member even with the device in the released position.
Maintenance
- Inspection of the Remote load release device is advised after each use.
- After use in or near sea water, a fresh water rinse of the Remote load release device is advised before it is stored.
- Pivot pins may require periodic re-lubrication.
Load Definitions
- Static Load: Forces solely due to the weight or gravity of objects being handled.
- Dynamic Load: A load created by motion of the object that increases or decreases the static load.
- Hydrodynamic Load: A load resulting from motion through the water including lift and drag.
- Inertial Load: A load resulting from accelerated releasing caused by tension on the object that is greater than gravity.
- Total Load: The sum of all above loads or forces acting on the object
Dimensions & Specifications
![]() |
|||||||||||
Part N° |
Recommended Shackle Size |
Dimensions (mm) | SWL (kg) | Break load (kg) | Weight (kg) | ||||||
Recommended shackle opening | Recommended shackle pin dia. | C | D | E | F | G | |||||
4193-T22955 | Keyring | -- | -- | 9.52 | 44.4 | -- | 4.76 | 31.75 | NOT RATED | 0.36 | |
4193-T22956 | 1/4" | 11.93 | 7.87 | 10.41 | 73.39 | 4.57 | 9.39 | 49.78 | 590 | 2,902 | 0.14 |
4193-T22957 | 7/16" | 19.05 | 12.7 | 17.52 | 114.3 | 6.35 | 13.97 | 79.5 | 1,450 | 7,529 | 0.58 |
4193-T22958 | 5/8" | 26.92 | 19.05 | 25.4 | 168.14 | 9.65 | 20.57 | 115.82 | 3,190 | 15,966 | 1.81 |
4193-T22959 | 3/4" | 31.75 | 22.09 | 30.22 | 195.07 | 10.92 | 23.62 | 140.46 | 4,330 | 21,708 | 2.85 |
4193-T22960 | 1" | 42.92 | 28.7 | 41.4 | 247.65 | 14.22 | 30.73 | 174.49 | 7,185 | 35,924 | 5.67 |
4193-T22961 | 1-3/8" | 57.15 | 38.1 | 53.84 | 334.01 | 19.05 | 41.4 | 232.41 | 12,700 | 63,502 | 14.5 |
4193-T22962 | 1-1/2" | 60.45 | 41.14 | 57.15 | 361.95 | 20.57 | 45.21 | 251.96 | 14,905 | 74,525 | 18.14 |
4193-T22963 | 1-3/4" | 73.15 | 50.8 | 69.85 | 446.02 | 25.4 | 54.86 | 310.13 | 22,770 | 113,851 | 31.2 |
4193-T22964 | 2" | 82.55 | 57.15 | 79.5 | 501.14 | 28.44 | 62.48 | 349.25 | 28,750 | 143,743 | 48.98 |
4193-T22965 | 2-1/2" | 104.9 | 69.85 | 98.55 | 612.9 | 34.79 | 76.45 | 426.97 | 42,970 | 214,866 | 89.35 |
4193-T22966 | 3" | 127 | 82.55 | 120.65 | 782.06 | 44.45 | 97.79 | 544.32 | 69,960 | 349,810 | 138.8 |
The Hook-Clamp consists of several moving parts that allow the 'jaw' to open and release a load, generally you would use a release line to attach to the lever, pull this line and the load will release.
Alternative Methods of Release
These are the alternative methods for releasing the shackle:
- Manually, pulling a long release line. No modification of the device is required. This method is used with lower capacity models, offers the lowest cost, and has many satisfied users.
- Hydraulically, using a winch and cable, such as used with a deck-mounted crane, to pay out the load against a secured release line. No modification of the device is required for this method.
- Hydraulically, paying out the load against a fixed-length, bulkhead-mounted release cable. Using a clevis instead of a shackle, a bulkhead-mounted hydraulic ram is attached to the rear end of the horizontally positioned devise to pull it back after the unit is locked. The release cable is then secured to the bulkhead and when release is desired, the hydraulic ram is actuated, allowing the Remote load release device to move toward the load and eventually against the secured release cable and the load releases the unit. This method allows the instalment of a pressure gauge into the hydraulic system to determine the actual tensile load being released. No modification of the device is required
- Explosive electric squib thrusters inserted into a special chamber below the toggle pin are used successfully to activate the device.
- Hydraulic pressure to drive a hydraulic cylinder to actuate the release lever of the Remote load release device is being used with the device ram models. These units can be activated by hydraulic hand pump, air-hydraulic foot pump, or electric pump.
- Air Cylinders provide another method of release and are fitted for activation using shop air at 60 to 100 PSI.
Device Locking
- Having secured the recommended shackle to the rear end of the Hook-Clamp (anchorage / top suspension eye), open the jaw by removing the hitch pin and lifting up the release lever and opening it to the released position. Insert the pin of the shackle to be released into the jaw opening.
- Secure the shackle by closing the release lever to the locked position and firmly lock the toggle pin over centre with a vice-grip-like snap.
- The shackle is now held firmly locked even with no load on the device. The safety pin (Hitch pin) can be reinserted to prevent inadvertent release.
- The Hook-Clamp is now ready to be loaded. Once the safety / hitch pin is removed, the Hook-Clamp is armed and ready to be released. Either to “set down” a load or to drop a load in a controlled manor (as a drop test / dropping clamp)
Device Releasing
Manual release of the loaded Hook-Clamp is activated by first removing the safety / hitch pin. This is done either manually (directly by hand) or by a pull cord attached to the spring loaded safety hitch pin; i.e. remotely and safety from a distance. The safety hitch pin release cord can be activated from any direction.
Once the safety hitch pin has been removed the clamp is “loaded” or “Live” and pulling the cord attached to the release lever WILL DROP / RELEASE the load. Pulling firmly on a release line connected to the end of the release lever also means that the operator can safety release the load away from the “danger area”. The release line can be activated “Directly” in any direction within the 90 degrees perpendicular and parallel to the line of load. The “Standard” release lever can also be operated from above the load as shown in the diagram below with the use of a suitable pulley; effectively giving 180 degree operation.
The Hook-Clamp can release the load with or without load on the unit. (providing the safety hitch pin is removed).
The use of the hitch pin is not required to secure the device in the locked position. It is an added, secondary safety measure preventing inadvertent release. A safety hitch pin is provided with each unit. The standard safety hitch pin is not spring loaded for remote operation (from distance by a pull cord).
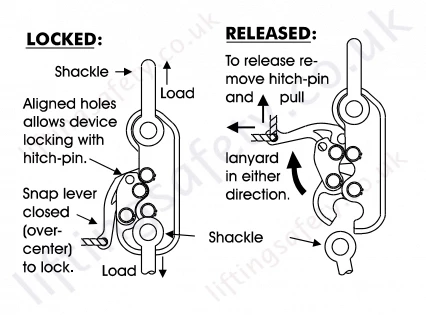
Capacities and Release Capacities.
Detailed below are the figures of the estimated effort required to release a load at full capacity. This effort can be adjusted by following the instructions below.
Safe Working Load | Estimated Effort To Pull Lanyard To Release Capacity Load (Can be adjusted, see below) |
590kg | 3.62kg |
1,507kg | 8.61kg |
3,194kg | 18.14kg |
4,342kg | 39.91kg |
7,186kg | 65.77kg |
12,776kg | 117kg |
14,902kg | 136.53kg |
22,770kg | 208kg |
28,747kg | 263kg |
42,975kg | 393kg |
69,960kg | 640kg |
Remote Load Release Device Hitch-Pin
The hitch pin can be supplied "Spring Loaded" remote triggered release. This means that the hitch pin can be remotely removed from the body of the Hook-Clamp by use a pull-cord attached to a spring loaded hitch pin and therefore ensuring an additional level of safety even when the operator cannot physically reach the hitch pin to physically release it!
Adjusting The Effort Required to Operate the Manual release lever (Remote load release device Over-Centre Pressure Adjustment)
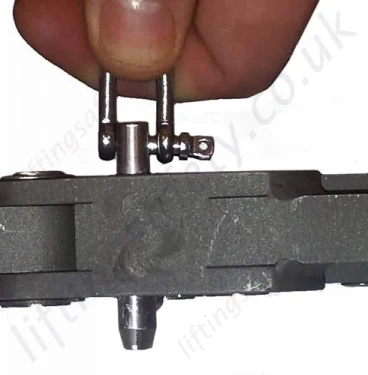
Standard Release Safety Pin Design
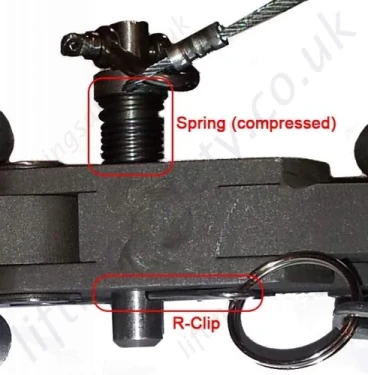
Spring Release Safety Pin R Clip Design
Ample material has been left at the tip of the movable jaw (see arrow) where the jaw and body come in contact. This aids in holding the device securely over-centre in the locked position even when no load is applied to the device. It also helps prevent inadvertent release of the device.
Should the user require that the effort to lock the release lever of the device over-centre be reduced, the procedure is to locate the area where the surface of the jaw comes in contact with the body and lightly file or grind off material in that area.
It is important to test the effort frequently after some material has been removed so as to prevent the removal of too much material.
Should the user require that the effort to lock the release lever of the device over-centre be increased, the procedure is to increase the thickness of the material between the two surfaces by applying a center punch mark in the area of the jaw where the surfaces meet. Should there still be insufficient material to ensure the positive locking integrity of the device, the contact area of the jaw will need to be spot-welded. This welded material will then need to be ground to the appropriate thickness.
Release Operation
Standard Release Lever | Reverse Release Lever | Standard Lever Release with Pulley (the same can be done with reverse lever if necessary) |
![]() |
![]() |
![]() |
You May Also Like
Contact Us About This Product
If you wish to receive a quote for this product, please use the tab above, this form is for general enquiries regarding this product only.
You can also Request a Quote using the Quote tab above!
You can easily add more than one item to the Quote Request. This is highly recommended as we will be able to suit your needs much more efficiently.