-
Lifting Equipment
Lifting Equipment
- Chain Hoists
-
Wire Rope Hoists & Winches
- Hand Operated Wire Rope Winches and Hoists
- Cable Pullers / Hoists, Wire Rope Manual Operation
- Electric Winches and Hoists, AC (Mains Powered)
- Scaffold Hoists & Accessories
- Overhead Wire Rope Crane Hoists
- Hydraulic Wire Rope Winches & Hoists
- Pneumatic Wire Rope Air Winches / Hoists (Lifting and Pulling)
- Vehicle Mounted Winches
- Tractel Wire Rope & Accessories
-
General Lifting Equipment
- Soft Lifting Slings
- Lifting Chain Slings
- Wire Rope Slings & Assemblies
- Lifting Shackles
- Eye Bolts and Nuts
- Weld-on Lifting Eyes and Lashing Points
- Lifting & Pulling Clamps
- Lifting Beams & Spreader Beams
- Precast Concrete Lifting
- Lifting Magnets, Permanent, Battery Electric and Manual
- Beam Trolleys and Crane Bridges, Push, Geared & Electric
- Equipment Identification Tags
-
Rigging Equipment
- Master Ring & Load Suspension Eyes
- Lifting & Rigging Hooks
- Turnbuckles & Rigging Screws
- Wire Rope Accessories and Fittings
- Snatch Blocks, Sheave Blocks and Crane Pulley Blocks
- Pulley Sheaves
- Lifting & Rigging Swivels - Eye, Hook & Shackle
- Load Restraint Equipment
- General Rigging Accessories
- Crosby Lifting & Rigging
-
Cranes & Gantry Systems
- Portable Davit Arms
- Swing Jib Cranes - Installed Floor & Wall Cranes
- Portable/Mobile Free-standing Swing Jib Cranes
- Aluminium Gantry Cranes
- Steel Gantry Cranes
- Fixed Steel Gantry Systems
- Shearlegs, Tripods & Quadpods
- Overhead Crane Systems
- Portable Shop-Floor/Workshop/Garage Cranes
- Counterbalance Floor, Workshop Cranes
- Scaffolding Runway Beam Systems
-
Material Handling & Jacking Equipment
- Machinery & Load Moving Skates
- Hydraulic Cylinders & Pumps
- Lifting Jacks
- Manhole Cover Lifters
- Hydraulic Pull Cylinders
- Hand Operated Pallet Trucks, Pump Trucks
- Stacker Trucks, Materials Lifts, Manual and Electric
- Genie and Counterbalance Materials Lifters
- Scissor Lift Tables
- Drum Handling Equipment
- Crane Forks
- Load Weighing Equipment - Load Cells
- Tool Spring Balancers / Load Balancers
- Platform Trucks & Trolleys
-
Forklift Truck Attachment
- Fork Mounted Man Riding Baskets
- Environment & Waste Handling Attachments
- Fork Lift Truck Mounted Drum Handling Attachments
- Fork Mounted Jib and Hook Attachments
- Fork Truck Booms & Tines
- Stainless Steel Forklift Attachments
- Forklift Truck Fork Extensions
- Multi Fork Attachments
- Fork Truck Scoop Attachments
- Big Bag Fork Truck Attachment
- Closed Base Coil Support Attachments
- Forklift Fork Protection Sleeves
- Snow Plough Fork Lift Truck Attachments
- Other Forklift Truck & Telehandler Attachments
- Specialist Lifting Equipment
- Access and Safety Related
- Workshop and Shop Floor
- Screwjacks & Actuators
-
Height Safety
Height Safety Equipment
-
Fall Arrest and Height Safety Harnesses
- General Use Harnesses EN361
- Work Positioning Harnesses EN361 & EN358
- Rope Access Harnesses
- Rescue Harnesses EN1497 & EN361
- Ladies & Childrens Harnesses
- Hi Vis Jacket/Vest Harnesses
- Welders Harnesses
- ATEX (Anti-Static) Harnesses
- Linesman Harnesses
- Oil Derrick Harnesses
- Sport Climbing Harnesses
- Tree Surgeon Positioning Harnesses
- Sit and Chest Harnesses. EN361 EN356 & EN831
- Work Positioning & Restraint Belts EN358
- Fall Arrest, Restraint and Positioning Lanyards
- Height Safety and Fall Arrest Kits
- Inertia Reels and Retrieval Blocks
-
Confined Space and Rescue Systems
- Xtirpa Confined Space Davit Arm Systems and Components
- Sala Advanced Davit Arm Systems and Components
- Genesi Confined Space Systems
- Abtech Man-riding, Fall Arrest and Rescue Davits and Components
- Man-riding Hoists & Rescue Winches
- Fall Arrest & Rescue Tripods
- Fall Arrest Davit Arms & Posts for Working at Height
-
Fall Arrest & Man-riding Systems
- Manriding Systems, Baskets and Chairs
- Mobile Fall Arrest Gantries, Systems & Steps
- Rope Guided Fall Arresters (Steel & Synthetic Rope)
- Temporary Horizontal Fall Arrest Lifelines
- Vertical Fall Arrest Systems Permanently Installed
- Horizontal Fall Arrest Systems Permanently Installed
- Manriding Baskets Fork Truck and Overhead Crane
- Tank Side Entry and Vehicle Fall Arrest Systems
- Suspension Seats / Bosuns Chair Working at Height
- Collective Fall Arrest Systems
- Man-Riding Sheave Blocks
- Anchorage Devices
- Karabiners & Connectors
- Rescue, Evacuation & Rope Access
-
General Height Safety Gear
- Height Safety Accessories
- Industrial & Climbing Height Safety Helmets
- Synthetic Height Safety Rope & Anchorage Lines
- Height safety Pulley Wheels For Synthetic & Steel Wire Rope
- Black Height Safety Equipment & PPE
- Hot Work Equipment. Cutting, Grinding & Welding
- Cases, Bags, Backpacks, Holdalls. Height Safety Gear
- Telescopic Extension Pole for Height Safety Applications
- Wind Energy Height Safety Equipment
- Stainless Steel Fall Arrest Equipment
-
Fall Arrest and Height Safety Harnesses
- Home
- About Us
-
Contact
Get In Touch
- Home/
- Lifting Equipment/
- Cranes; Mobile, Portable and Fixed/
- Swing Jib Cranes - Installed Floor & Wall Cranes/
- Column Mounted (Post), Free Standing Swing Jib Cranes/
- Donati GBA C3/4 'C' Profile Overbraced Jib Crane - upto 1000kg SWL
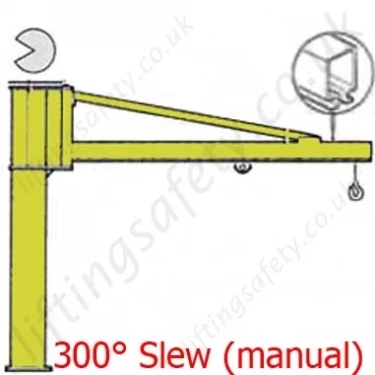
Donati GBA C3/4 'C' Profile Overbraced Jib Crane - upto 1000kg SWL
300° Manual Slew C-Profile Channel profile Free Standing Swing Jib Crane with Overbraced Arm.
Donati GBA C3/4 / PAUT1-975
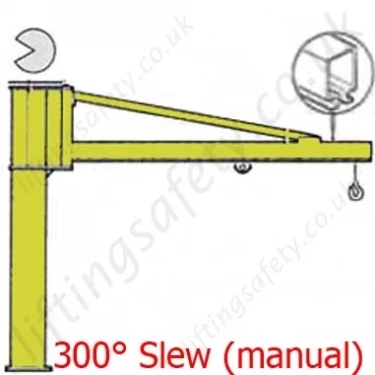
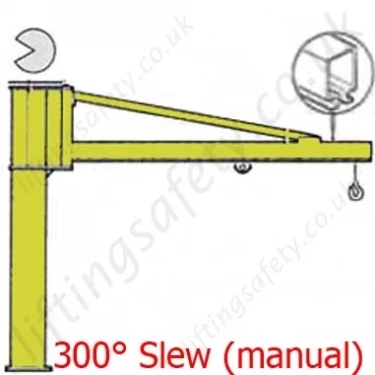
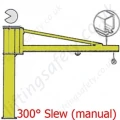
“C” Channel version:
- For lifting capacities from 63kg to 1000kg
- Jibs from 2m to 7m
- Manually rotated
- 300° Slew
- The arm is made using a special section bar made of folded sheet metal, inside which the hoist-carrying trolley runs.
- The arm is fitted with one or two staybolts which support the profile and connect it to the rotation tube.
- This version is characterised by the extreme ease of handling due to the low inertia derived from its own reduced weight.
- The arm is normally fitted with a special “channel” profile trolley, which allows it to be pushed with maximum fluidity.
- Our jib cranes are designed and manufactured according to the ISO A5 classification.
The manually rotated jib cranes in this series are designed for the handling of goods inside a plant, in a square or to serve operative positions. The standard models are available for lifting capacities from 63kg to 2000kg and jibs from 2m to 8m The C version (this page, see above); T versions and H versions are designed according to the three different versions of the arm.
The column crane can be supplied, on request, with a main on/off line switch which can be padlocked. The distribution of energy takes place via a flat festoon cable which slides on trolley along the arm.
Dimensions
Lifting Capacity (KG) | Arm (S) Nominal (M) |
True Length (MM) |
Size of Jib Crane Bracket |
Column |
Total Height H (M) Base |
Type |
Under Beam h |
G | L | M | N | Δ | Weight Crane (KG) |
Column by M |
63 | 4 | 4056 | A | R | 3 | C30R40 | 2496 | 228 | 34 | 140 | 585 | 12 | 127 | 18.2 |
5 | 5056 | A | R | 3 | C30R50 | 2496 | 228 | 34 | 140 | 645 | 12 | 140 | 18.2 | |
6 | 6056 | B | S | 3 | C30S60 | 2496 | 274 | 34 | 140 | 705 | 12 | 175 | 22.8 | |
7 | 7056 | B | S | 3 | C30S70 | 2496 | 274 | 34 | 140 | 765 | 12 | 188 | 22.8 | |
125 | 2 | 2056 | A | R | 3 | C30R20 | 2496 | 228 | 34 | 140 | 525 | 12 | 101 | 18.2 |
3 | 3056 | A | R | 3 | C30R30 | 2496 | 228 | 34 | 140 | 585 | 12 | 114 | 18.2 | |
4 | 4056 | B | S | 3 | C30S40 | 2496 | 274 | 34 | 140 | 585 | 12 | 149 | 22.8 | |
5 | 5056 | B | S | 3 | C30S50 | 2496 | 274 | 34 | 140 | 645 | 12 | 162 | 22.8 | |
6 | 6066 | C | T | 3.5 | C35T60 | 2738 | 323 | 34 | 140 | 785 | 17 | 260 | 35 | |
7 | 7066 | C | T | 3.5 | C35T70 | 2738 | 323 | 34 | 140 | 845 | 17 | 275 | 35 | |
250 | 2 | 2056 | B | S | 3 | C30S20 | 2496 | 274 | 34 | 140 | 525 | 12 | 123 | 22.8 |
3 | 3056 | B | S | 3 | C30S30 | 2496 | 274 | 34 | 140 | 585 | 12 | 136 | 22.8 | |
4 | 4066 | C | T | 3.5 | C35T40 | 2738 | 323 | 34 | 140 | 665 | 17 | 230 | 35 | |
5 | 5066 | C | T | 3.5 | C35T50 | 2738 | 323 | 34 | 140 | 725 | 17 | 245 | 35 | |
6 | 6066 | D | U | 3.5 | C35U60 | 2738 | 386 | 43 | 156 | 820 | 17 | 376 | 43.5 | |
7 | 7066 | D | U | 3.5 | C35U70 | 2738 | 386 | 43 | 156 | 880 | 17 | 402 | 43.5 | |
500 | 2 | 2066 | C | T | 3.5 | C35T20 | 2738 | 323 | 34 | 265 | 730 | 17 | 200 | 35 |
3 | 3066 | C | T | 3.5 | C35T30 | 2738 | 323 | 34 | 265 | 790 | 17 | 215 | 35 | |
4 | 4066 | D | U | 3.5 | C35U40 | 2738 | 386 | 34 | 265 | 820 | 17 | 287 | 43.5 | |
5 | 5066 | D | U | 3.5 | C35U50 | 2738 | 386 | 34 | 265 | 880 | 17 | 303 | 43.5 | |
6 | 6076 | E | V | 4 | C40V60 | 2980 | 443 | 43 | 156 | 880 | 20 | 567 | 64 | |
7 | 7076 | E | V | 4 | C40V70 | 2980 | 443 | 43 | 156 | 940 | 20 | 597 | 64 | |
1000 | 2 | 2066 | D | U | 3.5 | C35U20 | 2738 | 386 | 60 | 306 | 790 | 17 | 267 | 43.5 |
3 | 3066 | D | U | 3.5 | C35U30 | 2738 | 386 | 60 | 306 | 850 | 17 | 337 | 43.5 | |
4 | 4076 | E | V | 4 | C40V40 | 2980 | 443 | 60 | 306 | 910 | 20 | 509 | 64 | |
5 | 5076 | E | V | 4 | C40V50 | 2980 | 443 | 60 | 306 | 970 | 20 | 538 | 64 | |
6 | 6076 | F | Z | 4 | C40Z60 | 2980 | 513 | 60 | 306 | 1100 | 20 | 680 | 75.2 | |
7 | 7076 | F | Z | 4 | C40Z70 | 2980 | 513 | 60 | 306 | 1160 | 20 | 713 | 75.2 |
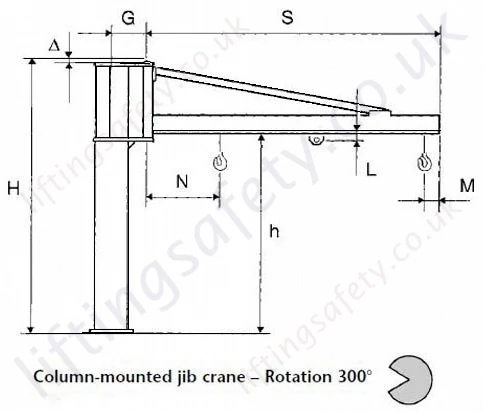
Swing Jib Crane Installation - Customer's responsibility:
Please note that these jibs priced on line are quoted as supply only. We believe that this will give you the most cost effective solution; your engineering staff or a local contractor could install at cheaper hourly rate than our lifting engineers and won't have the travel time that we would incur. If any civil works are required to the floor (or support structure) it would be best (and cheaper) done by Civil Engineering Company (or Fabricator), after all this is their area of expertise. We would be please to offer a price for installation on request.
- Installation quotes, unless otherwise specified, include for working in a clear uninterrupted site with good access, during normal working hours. Other times can be negotiated to suit your requirements. Site delays due to obstructions would be chargeable extras. Check there are no obvious defects on the support structures and the fixing;- check the suitability of the maneuvering areas (rotation) available to the jib crane,especially if it operates in areas where there are other cranes and manufacturing machines
- For our enginners to install the jib crane we would require the use of your fork truck / overhead crane & operator to unload and install (Refers to quotes for Installation Only)
- The client must provide a suitable power supply to an appropriate position and make all electrical connections into the power isolator. Check the suitability and the correct functioning of the electrical power supply:
1) correspondence between the voltage of the power line with the voltage for the motors
2) that there is a suitable switch, selector of the electric line;
3) adequacy of the section of cable of the electric power line;
4) the presence and suitability of the earthing system - Where our engineers work involves the drilling into existing concrete structures, it is assumed that this drilling will not be effected by reinforcement bars. If such an obstruction is met on site, we reserve the right to charge extra for any costs such as labor or special drilling equipment, again this refers to quotes for Installation Only
- Unless otherwise quoted / specified and formally agreed our quote for a swing jib crane will not include for the Installation and load deflection test (please advise if you would like us to give a quote)
- The customer / installer must ensure suitability of your existing concrete floor / support structure (adequacy for loading, foundation requirements and leveling) when bolting onto directly to existing floor or building, we could provide a complete survey, at an additional cost, if required.
Or
- Carry-out civil / engineering works to provide a suitable foundation for the jib crane to be mounted.
- The check of the suitability of the anchorings to the pillar or to the floor as well as the sizing of the plinths must always be carried out by
expert, qualified technicians who will formally assume their responsibilities. - The installation of the jib crane, for the importance of the operations, if not carried out correctly can cause serious risks for the safety of people nearby in the assembly stage and the successive phase of use of the crane.In any case this task must be entrusted to specialised installers for the assembly of industrial systems, following careful evaluation of the following parameters:
- environmental characteristics of the place of work (e.g.working surface,etc)
- height of the work level at a height with respect to the load level
- dimensions and weight of the parts to be installed
- available space for the handling of the parts to be installed. - Before proceeding to the assembly of the parts and to to the putting into action of the jib crane, the installer must ensure that the characteristics of the crane are adequate to the use which it is intended for and in particular:
1) the lifting capacity of the crane is ≥ with respect to the loads to lift.
2) the characteristics of the fixing structures (plinth, floor, wall, pillar,etc.) have been “declared suitable” by the user or by expert technicians, engaged by the user.
3) the characteristics of the lifting unit (trolley/hoist), if not part of the supply, are compatible with those of the jib crane in relation to:
a. Lifting capacity of the hoist: must be ≤ with respect to the lifting capacity of the jib crane.
b. Weight of the trolley/hoist: must be ≤ with respect to the maximum ones intended
c. Lifting/moving speed: must be ≤ with respect to the maximum ones allowed.
d. Headroom of the figure of the hoist trolley: must be ≤ with respect to those allowed.
e. Reactions on the trolley wheels: must be ≤ with respect to the maximum ones allowed. - In the case of the jib crane with laminate girder, check the width of the wing of the girder which must correspond to that intended for the wheels of the trolley. Following the installation activities of the jib cranes, it is the precise duty of the installer to:
1) lead the activities of the putting into service as described in the manual of “Instructions for use”
2) fill in the report of the “check and correct installation” of the crane, deliberating over the “suitability for use”
3) take care of the complete editing of the responsibility of parts as intended in the checks register.
Oversized Base Plate/CounterPlate (Bolting To Existing Floor)
This is designed to spread the load when bolted to a suitable existing concrete floor. Refer below for manufacturers minimum recommended floor thickness.
Counter Plate Type | R | S | T | U | V | Z | |
Counterplate Dimensions (mm) |
C | 400 | 450 | 500 | 600 | 800 | 950 |
S | 20 | 25 | 25 | 30 | 35 | 45 | |
X | 330 | 195 | 220 | 180 | 182 | 220 | |
Y / Y1 | - | - | - | - | - | 240 / 248 | |
Nr x Dia. | 4 x 15 | 8 x 15 | 8 x 19 | 12 x 19 | 16 x 25 | 28 x 25 | |
Counterplate Weight (kg) | 20 | 31 | 39 | 63 | 139 | 254 | |
Maximum tilting movement allowed (kNm) | 11,8 | 20,7 | 31,2 | 56,7 | 107,3 | 164 | |
Type of concrete of the floor: Class Rck minimum (kg/cm2) | C250 | C250 | C250 | C250 | C250 | C250 | |
Minimum thickness of floor block (mm) | 140 | 170 | 170 | 220 | 220 | 220 | |
Diameter of hole in the floor (mm) | 14 | 14 | 18 | 18 | 24 | 24 | |
Depth of the hole of the concrete in the floor (mm) | 110 | 110 | 125 | 125 | 170 | 170 | |
Clamping torques of the bolts (Nm) | 40 | 40 | 80 | 80 | 150 | 150 | |
Project resistance of traction of one bolt (kN) | 25,3 | 25,3 | 40 | 40 | 74,6 | 74,6 |
The fixing of the column using chemical bolts, needs a scrupulous check of suitability in relation to the type of support flooring.
The suitability checks are the responsibility of the user and must be carried out by expert, qualified technicians who will evaluate the feasibility and formally undertake the relative responsibilities.
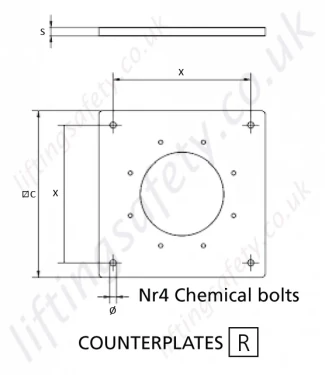
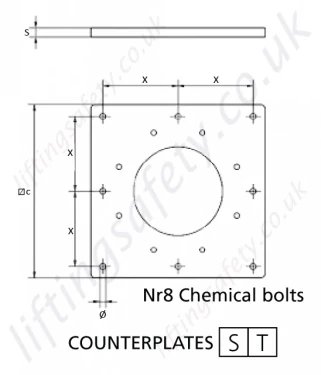
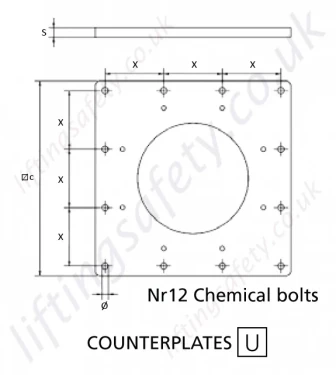
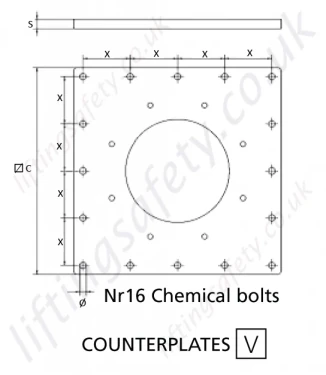
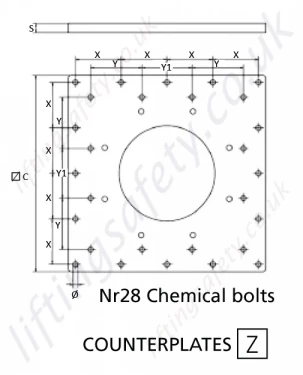
Base Plate Specifications
Note: The foundation frame with logbolts, used in the column-mounted version for fixing the column itself to the foundation plinth is supplied on request.
Size of Jib Crane | R | S | T | U | V | Z |
Base Plate and Foundation Frame (mm) | ||||||
C | 205 | 258 | 296 | 372 | 435 | 515 |
P | 275 | 340 | 380 | 475 | 555 | 660 |
S1 | 15 | 15 | 15 | 20 | 20 | 25 |
S2 | 8 | 8 | 8 | 8 | 8 | 8 |
X | 247 | 305 | 345 | 432 | 506 | 599 |
Y | 103 | 126 | 143 | 179 | 210 | 248 |
Ø | 268 | 330 | 373 | 468 | 548 | 648 |
R | 88 | 104 | 116 | 145 | 165 | 197 |
Ø1 | 16 | 20 | 20 | 25 | 29 | 35 |
Ø2 | 13 | 17 | 17 | 21 | 25 | 31 |
Anchorage Bolts | ||||||
ØT | M12 | M16 | M16 | M20 | M24 | M30 |
LT | 400 | 450 | 450 | 550 | 600 | 700 |
ST | 40 | 45 | 45 | 55 | 60 | 75 |
Clamping Couples (Nm) | 45 | 105 | 105 | 200 | 350 | 680 |
Frame/Bolts Weight (kg) | 5 | 10 | 11 | 17 | 26 | 47 |
Foundation | ||||||
Foundation Plinth (mm) (L) | 1200 | 1300 | 1400 | 1700 | 2000 | 2400 |
Foundation Plinth (H) | 800 | 800 | 900 | 900 | 1100 | 1100 |
Reaction (kN) Q1 | 3.3 | 5.7 | 10.15 | 18.4 | 28.7 | 29.35 |
Momentum (kNm) MF | 10 | 16 | 30 | 56 | 107 | 163 |

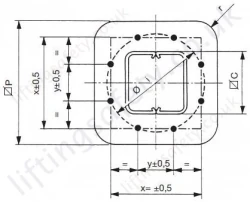
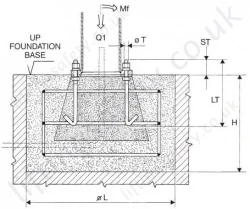
Pricing
“C” Channel version:
- For lifting capacities from 63kg to 1000kg
- Jibs from 2m to 7m
- Manually rotated
- 300° Slew
- The arm is made using a special section bar made of folded sheet metal, inside which the hoist-carrying trolley runs.
- The arm is fitted with one or two staybolts which support the profile and connect it to the rotation tube.
- This version is characterised by the extreme ease of handling due to the low inertia derived from its own reduced weight.
- The arm is normally fitted with a special “channel” profile trolley, which allows it to be pushed with maximum fluidity.
- Our jib cranes are designed and manufactured according to the ISO A5 classification.
The manually rotated jib cranes in this series are designed for the handling of goods inside a plant, in a square or to serve operative positions. The standard models are available for lifting capacities from 63kg to 2000kg and jibs from 2m to 8m The C version (this page, see above); T versions and H versions are designed according to the three different versions of the arm.
The column crane can be supplied, on request, with a main on/off line switch which can be padlocked. The distribution of energy takes place via a flat festoon cable which slides on trolley along the arm.
Dimensions
Lifting Capacity (KG) | Arm (S) Nominal (M) |
True Length (MM) |
Size of Jib Crane Bracket |
Column |
Total Height H (M) Base |
Type |
Under Beam h |
G | L | M | N | Δ | Weight Crane (KG) |
Column by M |
63 | 4 | 4056 | A | R | 3 | C30R40 | 2496 | 228 | 34 | 140 | 585 | 12 | 127 | 18.2 |
5 | 5056 | A | R | 3 | C30R50 | 2496 | 228 | 34 | 140 | 645 | 12 | 140 | 18.2 | |
6 | 6056 | B | S | 3 | C30S60 | 2496 | 274 | 34 | 140 | 705 | 12 | 175 | 22.8 | |
7 | 7056 | B | S | 3 | C30S70 | 2496 | 274 | 34 | 140 | 765 | 12 | 188 | 22.8 | |
125 | 2 | 2056 | A | R | 3 | C30R20 | 2496 | 228 | 34 | 140 | 525 | 12 | 101 | 18.2 |
3 | 3056 | A | R | 3 | C30R30 | 2496 | 228 | 34 | 140 | 585 | 12 | 114 | 18.2 | |
4 | 4056 | B | S | 3 | C30S40 | 2496 | 274 | 34 | 140 | 585 | 12 | 149 | 22.8 | |
5 | 5056 | B | S | 3 | C30S50 | 2496 | 274 | 34 | 140 | 645 | 12 | 162 | 22.8 | |
6 | 6066 | C | T | 3.5 | C35T60 | 2738 | 323 | 34 | 140 | 785 | 17 | 260 | 35 | |
7 | 7066 | C | T | 3.5 | C35T70 | 2738 | 323 | 34 | 140 | 845 | 17 | 275 | 35 | |
250 | 2 | 2056 | B | S | 3 | C30S20 | 2496 | 274 | 34 | 140 | 525 | 12 | 123 | 22.8 |
3 | 3056 | B | S | 3 | C30S30 | 2496 | 274 | 34 | 140 | 585 | 12 | 136 | 22.8 | |
4 | 4066 | C | T | 3.5 | C35T40 | 2738 | 323 | 34 | 140 | 665 | 17 | 230 | 35 | |
5 | 5066 | C | T | 3.5 | C35T50 | 2738 | 323 | 34 | 140 | 725 | 17 | 245 | 35 | |
6 | 6066 | D | U | 3.5 | C35U60 | 2738 | 386 | 43 | 156 | 820 | 17 | 376 | 43.5 | |
7 | 7066 | D | U | 3.5 | C35U70 | 2738 | 386 | 43 | 156 | 880 | 17 | 402 | 43.5 | |
500 | 2 | 2066 | C | T | 3.5 | C35T20 | 2738 | 323 | 34 | 265 | 730 | 17 | 200 | 35 |
3 | 3066 | C | T | 3.5 | C35T30 | 2738 | 323 | 34 | 265 | 790 | 17 | 215 | 35 | |
4 | 4066 | D | U | 3.5 | C35U40 | 2738 | 386 | 34 | 265 | 820 | 17 | 287 | 43.5 | |
5 | 5066 | D | U | 3.5 | C35U50 | 2738 | 386 | 34 | 265 | 880 | 17 | 303 | 43.5 | |
6 | 6076 | E | V | 4 | C40V60 | 2980 | 443 | 43 | 156 | 880 | 20 | 567 | 64 | |
7 | 7076 | E | V | 4 | C40V70 | 2980 | 443 | 43 | 156 | 940 | 20 | 597 | 64 | |
1000 | 2 | 2066 | D | U | 3.5 | C35U20 | 2738 | 386 | 60 | 306 | 790 | 17 | 267 | 43.5 |
3 | 3066 | D | U | 3.5 | C35U30 | 2738 | 386 | 60 | 306 | 850 | 17 | 337 | 43.5 | |
4 | 4076 | E | V | 4 | C40V40 | 2980 | 443 | 60 | 306 | 910 | 20 | 509 | 64 | |
5 | 5076 | E | V | 4 | C40V50 | 2980 | 443 | 60 | 306 | 970 | 20 | 538 | 64 | |
6 | 6076 | F | Z | 4 | C40Z60 | 2980 | 513 | 60 | 306 | 1100 | 20 | 680 | 75.2 | |
7 | 7076 | F | Z | 4 | C40Z70 | 2980 | 513 | 60 | 306 | 1160 | 20 | 713 | 75.2 |
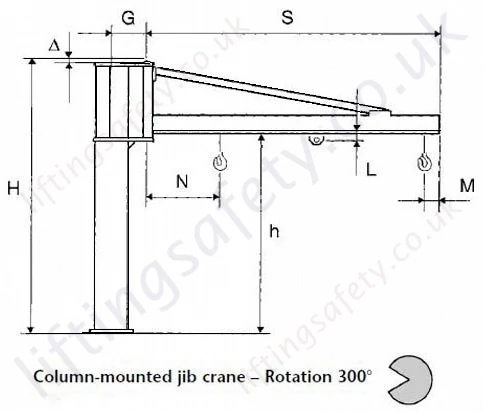
Swing Jib Crane Installation - Customer's responsibility:
Please note that these jibs priced on line are quoted as supply only. We believe that this will give you the most cost effective solution; your engineering staff or a local contractor could install at cheaper hourly rate than our lifting engineers and won't have the travel time that we would incur. If any civil works are required to the floor (or support structure) it would be best (and cheaper) done by Civil Engineering Company (or Fabricator), after all this is their area of expertise. We would be please to offer a price for installation on request.
- Installation quotes, unless otherwise specified, include for working in a clear uninterrupted site with good access, during normal working hours. Other times can be negotiated to suit your requirements. Site delays due to obstructions would be chargeable extras. Check there are no obvious defects on the support structures and the fixing;- check the suitability of the maneuvering areas (rotation) available to the jib crane,especially if it operates in areas where there are other cranes and manufacturing machines
- For our enginners to install the jib crane we would require the use of your fork truck / overhead crane & operator to unload and install (Refers to quotes for Installation Only)
- The client must provide a suitable power supply to an appropriate position and make all electrical connections into the power isolator. Check the suitability and the correct functioning of the electrical power supply:
1) correspondence between the voltage of the power line with the voltage for the motors
2) that there is a suitable switch, selector of the electric line;
3) adequacy of the section of cable of the electric power line;
4) the presence and suitability of the earthing system - Where our engineers work involves the drilling into existing concrete structures, it is assumed that this drilling will not be effected by reinforcement bars. If such an obstruction is met on site, we reserve the right to charge extra for any costs such as labor or special drilling equipment, again this refers to quotes for Installation Only
- Unless otherwise quoted / specified and formally agreed our quote for a swing jib crane will not include for the Installation and load deflection test (please advise if you would like us to give a quote)
- The customer / installer must ensure suitability of your existing concrete floor / support structure (adequacy for loading, foundation requirements and leveling) when bolting onto directly to existing floor or building, we could provide a complete survey, at an additional cost, if required.
Or
- Carry-out civil / engineering works to provide a suitable foundation for the jib crane to be mounted.
- The check of the suitability of the anchorings to the pillar or to the floor as well as the sizing of the plinths must always be carried out by
expert, qualified technicians who will formally assume their responsibilities. - The installation of the jib crane, for the importance of the operations, if not carried out correctly can cause serious risks for the safety of people nearby in the assembly stage and the successive phase of use of the crane.In any case this task must be entrusted to specialised installers for the assembly of industrial systems, following careful evaluation of the following parameters:
- environmental characteristics of the place of work (e.g.working surface,etc)
- height of the work level at a height with respect to the load level
- dimensions and weight of the parts to be installed
- available space for the handling of the parts to be installed. - Before proceeding to the assembly of the parts and to to the putting into action of the jib crane, the installer must ensure that the characteristics of the crane are adequate to the use which it is intended for and in particular:
1) the lifting capacity of the crane is ≥ with respect to the loads to lift.
2) the characteristics of the fixing structures (plinth, floor, wall, pillar,etc.) have been “declared suitable” by the user or by expert technicians, engaged by the user.
3) the characteristics of the lifting unit (trolley/hoist), if not part of the supply, are compatible with those of the jib crane in relation to:
a. Lifting capacity of the hoist: must be ≤ with respect to the lifting capacity of the jib crane.
b. Weight of the trolley/hoist: must be ≤ with respect to the maximum ones intended
c. Lifting/moving speed: must be ≤ with respect to the maximum ones allowed.
d. Headroom of the figure of the hoist trolley: must be ≤ with respect to those allowed.
e. Reactions on the trolley wheels: must be ≤ with respect to the maximum ones allowed. - In the case of the jib crane with laminate girder, check the width of the wing of the girder which must correspond to that intended for the wheels of the trolley. Following the installation activities of the jib cranes, it is the precise duty of the installer to:
1) lead the activities of the putting into service as described in the manual of “Instructions for use”
2) fill in the report of the “check and correct installation” of the crane, deliberating over the “suitability for use”
3) take care of the complete editing of the responsibility of parts as intended in the checks register.
Oversized Base Plate/CounterPlate (Bolting To Existing Floor)
This is designed to spread the load when bolted to a suitable existing concrete floor. Refer below for manufacturers minimum recommended floor thickness.
Counter Plate Type | R | S | T | U | V | Z | |
Counterplate Dimensions (mm) |
C | 400 | 450 | 500 | 600 | 800 | 950 |
S | 20 | 25 | 25 | 30 | 35 | 45 | |
X | 330 | 195 | 220 | 180 | 182 | 220 | |
Y / Y1 | - | - | - | - | - | 240 / 248 | |
Nr x Dia. | 4 x 15 | 8 x 15 | 8 x 19 | 12 x 19 | 16 x 25 | 28 x 25 | |
Counterplate Weight (kg) | 20 | 31 | 39 | 63 | 139 | 254 | |
Maximum tilting movement allowed (kNm) | 11,8 | 20,7 | 31,2 | 56,7 | 107,3 | 164 | |
Type of concrete of the floor: Class Rck minimum (kg/cm2) | C250 | C250 | C250 | C250 | C250 | C250 | |
Minimum thickness of floor block (mm) | 140 | 170 | 170 | 220 | 220 | 220 | |
Diameter of hole in the floor (mm) | 14 | 14 | 18 | 18 | 24 | 24 | |
Depth of the hole of the concrete in the floor (mm) | 110 | 110 | 125 | 125 | 170 | 170 | |
Clamping torques of the bolts (Nm) | 40 | 40 | 80 | 80 | 150 | 150 | |
Project resistance of traction of one bolt (kN) | 25,3 | 25,3 | 40 | 40 | 74,6 | 74,6 |
The fixing of the column using chemical bolts, needs a scrupulous check of suitability in relation to the type of support flooring.
The suitability checks are the responsibility of the user and must be carried out by expert, qualified technicians who will evaluate the feasibility and formally undertake the relative responsibilities.
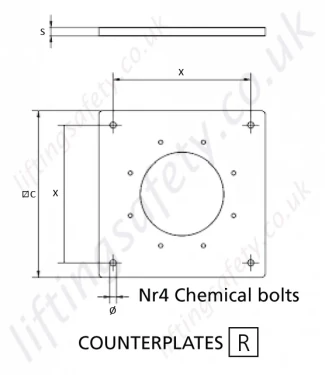
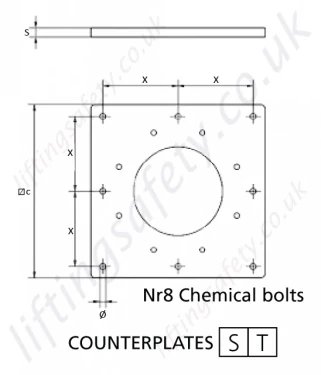
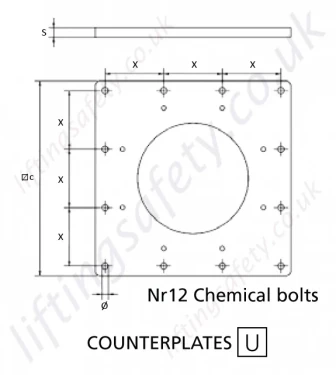
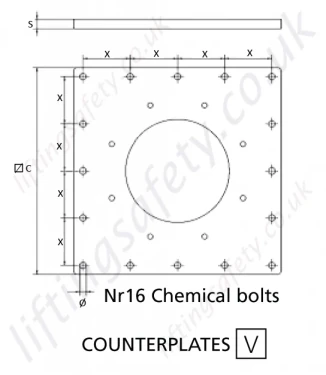
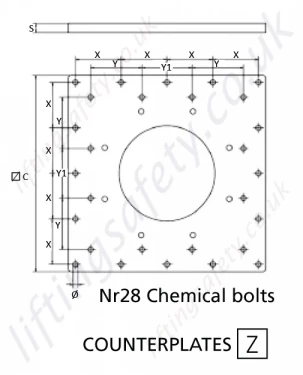
Base Plate Specifications
Note: The foundation frame with logbolts, used in the column-mounted version for fixing the column itself to the foundation plinth is supplied on request.
Size of Jib Crane | R | S | T | U | V | Z |
Base Plate and Foundation Frame (mm) | ||||||
C | 205 | 258 | 296 | 372 | 435 | 515 |
P | 275 | 340 | 380 | 475 | 555 | 660 |
S1 | 15 | 15 | 15 | 20 | 20 | 25 |
S2 | 8 | 8 | 8 | 8 | 8 | 8 |
X | 247 | 305 | 345 | 432 | 506 | 599 |
Y | 103 | 126 | 143 | 179 | 210 | 248 |
Ø | 268 | 330 | 373 | 468 | 548 | 648 |
R | 88 | 104 | 116 | 145 | 165 | 197 |
Ø1 | 16 | 20 | 20 | 25 | 29 | 35 |
Ø2 | 13 | 17 | 17 | 21 | 25 | 31 |
Anchorage Bolts | ||||||
ØT | M12 | M16 | M16 | M20 | M24 | M30 |
LT | 400 | 450 | 450 | 550 | 600 | 700 |
ST | 40 | 45 | 45 | 55 | 60 | 75 |
Clamping Couples (Nm) | 45 | 105 | 105 | 200 | 350 | 680 |
Frame/Bolts Weight (kg) | 5 | 10 | 11 | 17 | 26 | 47 |
Foundation | ||||||
Foundation Plinth (mm) (L) | 1200 | 1300 | 1400 | 1700 | 2000 | 2400 |
Foundation Plinth (H) | 800 | 800 | 900 | 900 | 1100 | 1100 |
Reaction (kN) Q1 | 3.3 | 5.7 | 10.15 | 18.4 | 28.7 | 29.35 |
Momentum (kNm) MF | 10 | 16 | 30 | 56 | 107 | 163 |

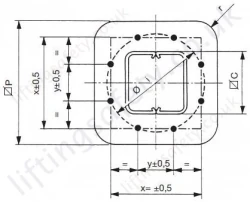
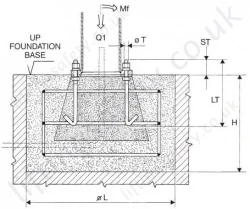
You May Also Like
Contact Us About This Product
If you wish to receive a quote for this product, please use the tab above, this form is for general enquiries regarding this product only.
You can also Request a Quote using the Quote tab above!
You can easily add more than one item to the Quote Request. This is highly recommended as we will be able to suit your needs much more efficiently.